With its combination of OEM expertise, industrial innovation and custom service, TAF is emerging as a new player to keep an eye on. The redesign of the TAF logo at the beginning of 2024 had already boosted the visibility of this new premium structure brand. Seduced by the range of these products, the distributor XLR joined forces with the manufacturer, serving France and the Benelux territory.
We set out for Olomouc, in Moravia (the eastern region of the Czech Republic), where I met up with Markéta Šimková and David Gore, two energetic marketing managers, for a guided tour of the factory and a detailed explanation from brand manager Pavel Zerotinsky.
When we arrived, the team was in a whirlwind of activity, with meetings, unforeseen events and a prefabricated building being set up in the central courtyard. “It’s intended to serve as the offices of the owner, the managing director, the accounts manager and the sales manager, because there isn’t enough space,” explains Pavel.
Here one can just feel the projects multiplying at this 100% European production facility. The TAF factory was founded 27 years ago. Drawing on the company’s experience in the OEM sector, it is developing its structure brand with the aim of consolidating its position in the high-end category. That’s all it took to win us over.
.
A proven structure for a new era in customised solutions
Several offices have been set up to handle distribution: TAF USA, TAF UK for the United Kingdom and Ireland, and the head office in the Czech Republic for Europe and the rest of the world, plus XLR in Belgium, the official distributor for France and the Benelux countries.
The brand emerges with compelling points in its favour. It’s backed by 27 years of experience in the field of OEM structures and state-of-the-art production equipment, including robotic welders and laser cutting machines. These major investments accelerate production times and ensure rapid response to made-to-order requests.
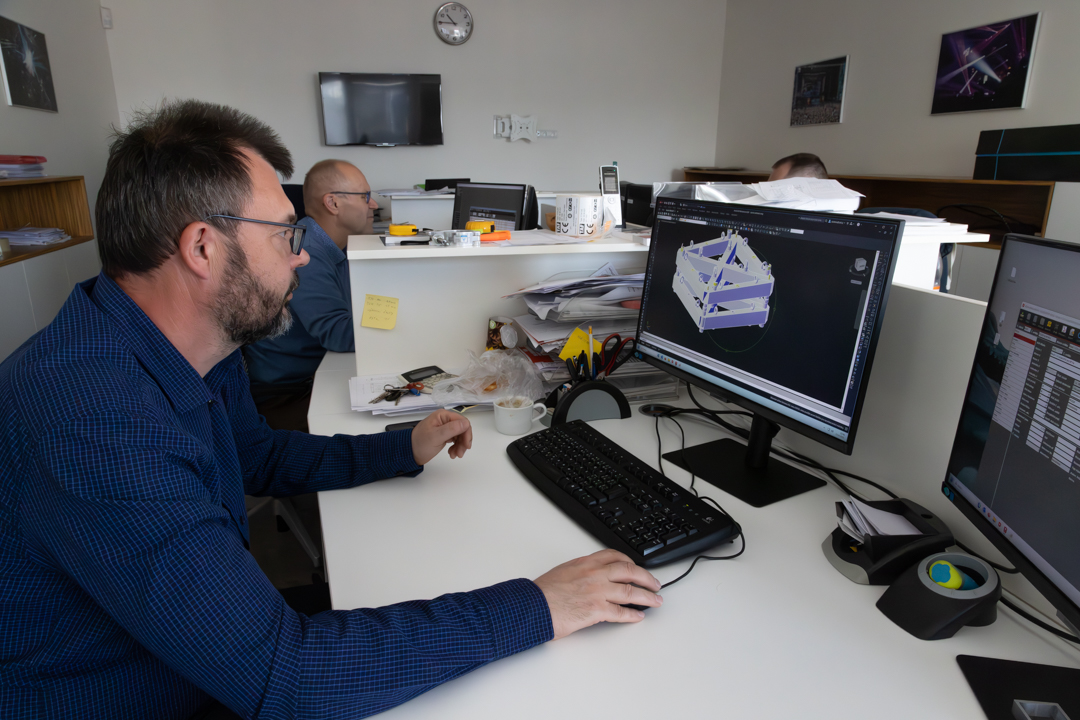
Customers can also rely on the support of a custom design and engineering department, a team of engineers whose job it is to model projects using 3D software, confirm them with the customer and adjust the specifications. “Once this stage has been validated, the sales team is then able to confirm production deadlines,” » explains Markéta :.
SLU: How does one place a custom order?
Markéta Šimková: This would depend on the requirements. Depending on how much customisation is involved in the project, the sales team will contact the technical department directly to determine the best way to design it. Our engineers work on technical drawings so that customers can check their project before it is manufactured. Once we receive confirmation, the order goes back to the sales department, which finalises the quote and consults with the production department to set a delivery date.
David Gore: It’s important to add that the team of engineers working on custom projects is also the team that develops all the structure and lifting products in the TAF catalogue. They are qualified engineers with extensive experience in this field. Having specialists work on our customers’ projects is one of our advantages.
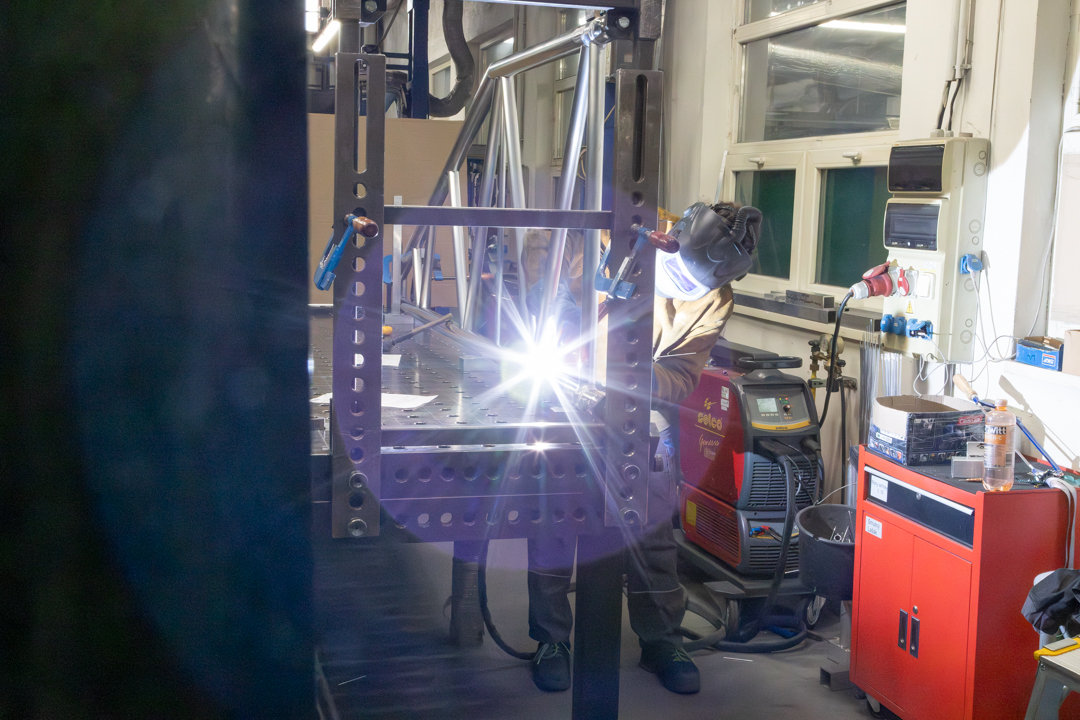
Truss On Time: Flexible production, with optimised stock and custom-made orders
Truss On Time is a promise to respect the delivery date established at the time of placing an order. When TAF confirms a delivery date, they stick to it.
Pieter Van Velde explains: “This concept involves two main working strategies. The first is that TAF has to be capable of reacting very quickly and manufacturing specific structural elements for custom projects, thanks to its flexibility in adapting its production lines. Compared with larger manufacturers, who have an inertia linked to minimum production quantities, TAF stays flexible.”
The second parameter of Truss On Time is TAF’s choice to work with distributors who keep an optimised stock. This means that at XLR we pay close attention to demand and how it evolves, and we are able to respond instantly to frequent requests.
SLU: What is the most in-demand item?
Pieter Van Velde: We are able to meet large orders for square-section 34 and 35 series (290 mm) trusses in black, as this is the product range for which there is currently the highest demand. Having said that, there may be some evolution in the types of connections required, so we make sure to pay close attention to the needs of XLR’s customers.
.
SLU: What is your approach to designing customised projects?
Pieter Van Velde: We can meet a large number of orders from stock, which means zero lead times. For customised orders, I provide support by studying the project with our customers and advising them, particularly on safety issues.
The team of engineers in the technical office can draw up load tables based on 3D modelling of projects. We can then estimate the impact of wind at different levels of force (Beaufort). This certification is mandatory in Germany, for example.
Assessing wind force in Beaufort means estimating the force exerted on an object by wind at speeds graduated according to the Beaufort scale. This empirical scale, from 0 to 12, is used mainly in meteorology and seafaring. It was created by the British admiral Francis Beaufort in the 19th century.
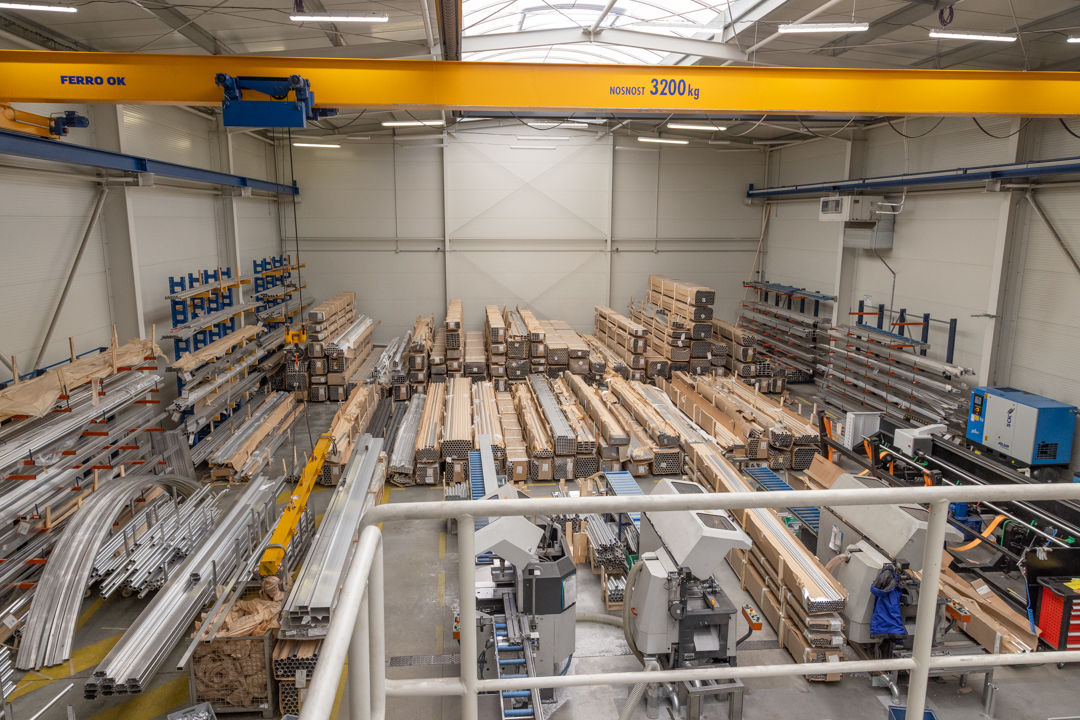
.
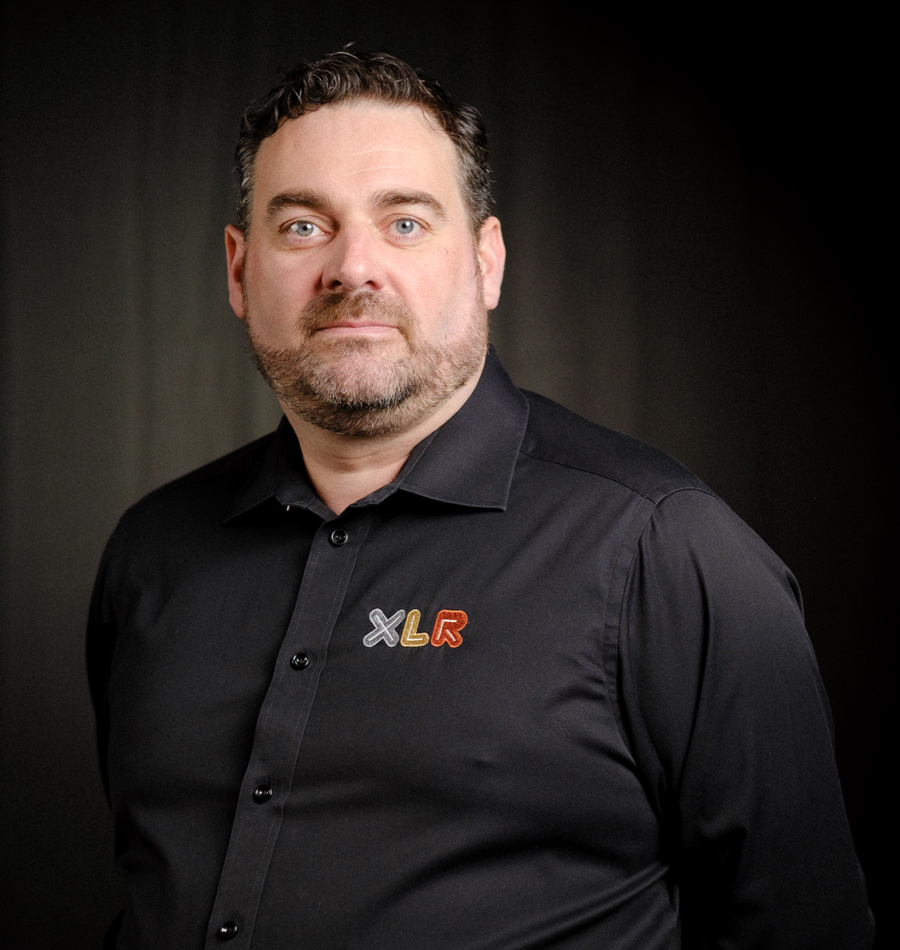
Pieter has been working in the entertainment sector for over 25 years. His experience has taken him successively into the roles of salesman, entrepreneur, brand manager, sales force manager and international business development manager. The AV industry is the common thread running through the career of this music enthusiast. As well as playing the keyboard, organ and piano, he has also been a DJ since he was 18.
At the beginning of 2024, he joined XLR to develop the company’s product range. “I initially came for the lighting,” recounts Pietre, “but very quickly we realised that there was a lack of structures/rigging in the catalogue. At the CUE trade show in Rotterdam, I met Milan at the TAF stand. That’s when we started talking about the possibility of creating a partnership”.
.
High-performance alloys, weld traceability and industrial automation at TAF
More than 95% of structures are made from EN-AW 6082 T6 grade alloy, the strongest to date for the manufacture of aluminium products. The EN-AW 6060 T66 alloy is specified for small, mainly ornamental structures that do not have to bear heavy loads. Raw materials are contracted out to suppliers chosen for the quality of their aluminium.
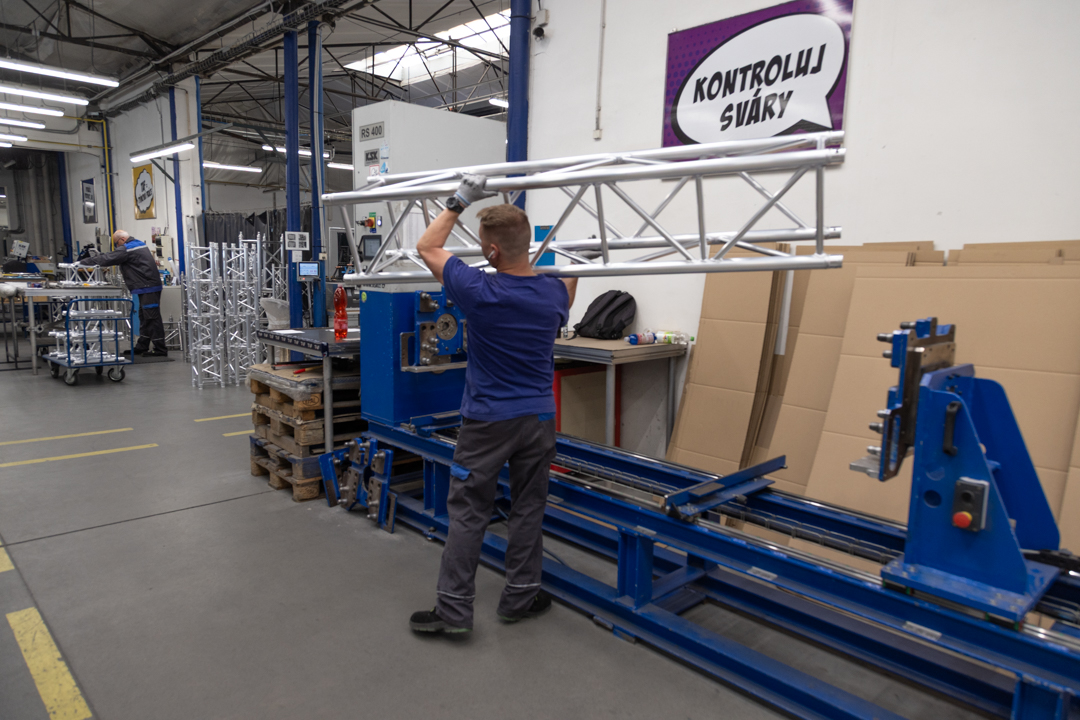
In addition to complying with load tests carried out every two years to obtain TÜV certification for the quality and strength of the welds produced at the Truss Aluminium Factory, the manufacturer’s welders receive special attention.
For the trussing and towers, they must be able to provide precise traceability, permitting the origin of the materials to be tracked, and the identity of the welders to be verified in the event of a problem, so that detailed investigations can be carried out.
.
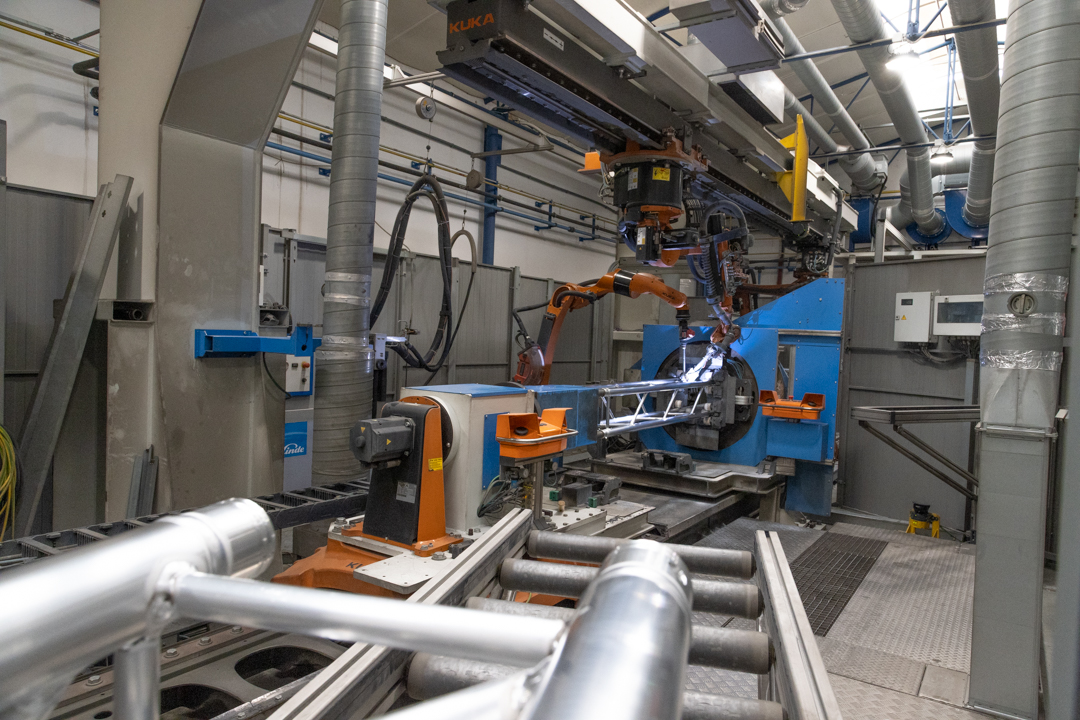
The welders are therefore highly experienced, and TAF has chosen to train its staff in-house, both to ensure the quality of the welds, which require specific skills, as well as to liberate itself from a tight labour market.
TAF has also chosen to invest in modernisation, equipping their production with robotic welding cells, which ensure both speed of execution and the consistent weld quality. The FT34 components benefit from this.
As part of a major investment programme, a new laser cutting machine has been added to the production facilities.
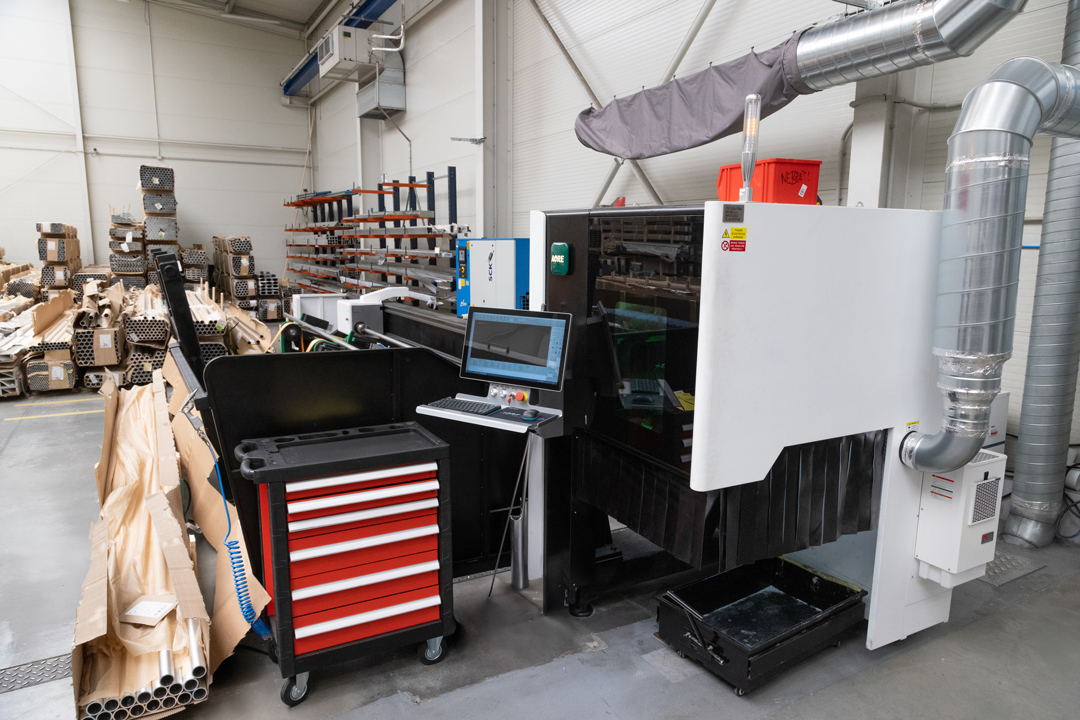
David Gore: This new machine makes it possible to cut the tubes required for corner elements more quickly.
Markéta Šimková : For example, sleeve blocks used to take around 40 minutes to produce, compared with 40 seconds with this machine.
One of the company’s goals is to innovate in production techniques to achieve the best possible quality with more efficient processes.
The TAF product range at a glance
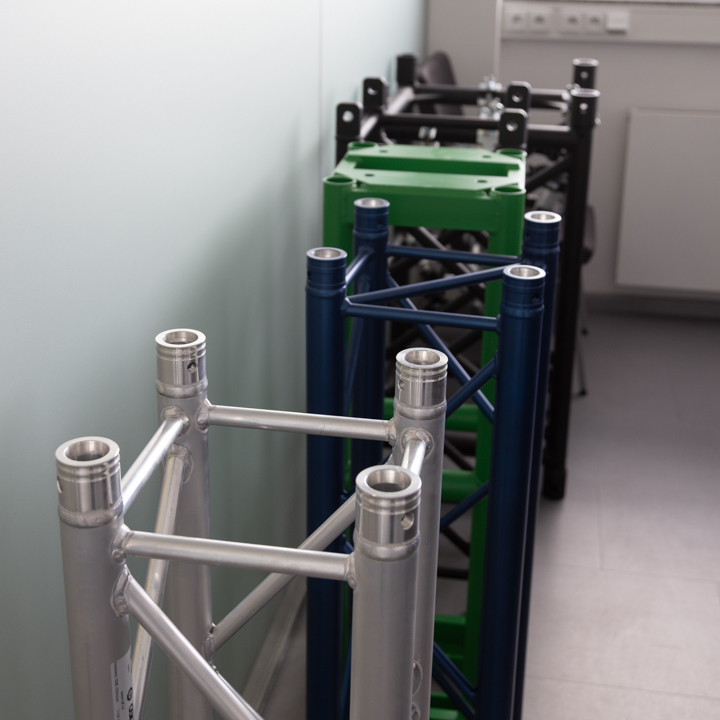
The catalogue offers a very wide range of products to meet all your lifting and rigging needs: trussing, pre-rig trussing, tower lifters, truss elevators, stage decks, stage roofs, self-supporting LED screen structures, as well as a wide range of accessories such as clamps, baseplates and totems.
TAF offers three truss connection systems:
– Classic “Quicklock” with conical ends + couplers + spigot pins
– Bolted plates: trusses with sheet metal sections welded to each end of the segments are secured with bolts and nuts
– The male/female forked-end system secured with a steel pin and a safety clip.
All the structures and systems in the catalogue are delivered with a connection kit as standard, whichever it may be, and each truss can be fitted with corner junctions to suit any configuration.
FT Truss
The FT range comprises five structural shapes – triangular, ladder, tube, square, rectangular – and no fewer than 27 lines of trusses that differ in shape, cross-section and strength, but all feature the same Quicklock rapid connection system. They can be ordered in any RAL finish you desire.
PT Truss
This range is designed to improve compatibility with other brands. The main truss chords have specific dimensions and the order, number and design of the braces are tailored to ensure compatibility. All of these use Quicklock connections.
ET Truss
The ET Truss is characterised by one of its chords, which features a special profile designed to accommodate a busbar power rail to facilitate the use track-lighting fixtures. These use Quicklock connections.
Bolted Truss
Very popular in the events sector, bolted truss sections have a sheet metal plate welded to each end. Each plate is pre-drilled and the segments are assembled using bolts and nuts. These are available in three different duties: light, medium and heavy.
Fork Truss
Comprising three series designed for grid support – Light-Duty, Medium-Duty and Heavy-Duty – the Fork/GS range is made up of high-strength chords and braces and uses an interlocking fork connection system. The male termination slides into the female connector and the joint is secured with a steel pin and safety clip.
Tower
These towers can be used to raise and support a PA system, an LED wall or grid, and are utilised in TAF roof and LED frame supports. They can be fitted with manual steel cable winches or chain hoist motors.
The range comprises eight models, differing in their maximum lifting height, from 6 to 20 metres, and in their maximum load capacity, from 350 kg to 5 tonnes, with special features such as the PA Tower 05, which is optimised for flying speaker arrays, thanks to the arched structure at the top.
.
Roofs
TAF offers a wide range of roof systems in all sizes and designs – Gable, Sloping, Arched, Pitched, Keder, Tunnel.
.
Tower lifters
From the smallest and lightest model, TLT 125, which is capable of lifting 125 kg to a height of 3.8 metres, to the TLT 300 that can lift 300 kg up to 6.5 m, there are five crank-up lifts with telescopic legs to meet any lifting requirement. The TLF 125 and TLF 270 are equipped with a steel lifting fork that can be loaded from the ground.
.
Freestanding LED frames
This is a range of four ready-to-use, free-standing gantries designed to support LED displays: 5 × 3 m, 6 × 4 m, 8 × 6 m, 10 × 8 m.
.
XLR, a new distributor for France and Benelux
Based just outside Brussels in Wemmel, Belgium, XLR has existed for just over 11 years. It grew out of the heritage of another well-known Belgian company in the sound sector: ASC. Louis Loukoussa and Yann De Brucker are the founders of XLR, and they have succeeded in perpetuating ASC’s heritage through the company’s catalogue and customer portfolio. As a distributor of products for the events industry, the company puts its faith in first-class service and equipment (L-Acoustics, Allen&Heath, Neumann, Sennheiser, Shure, as well as Minuit Une and Elation) to differentiate itself from its parent company.
Luka Lukusa, Marketing Director, explains: “XLR is not in the business of distributing equipment, but rather at the service of events, shows and the experience that people are going to have”.
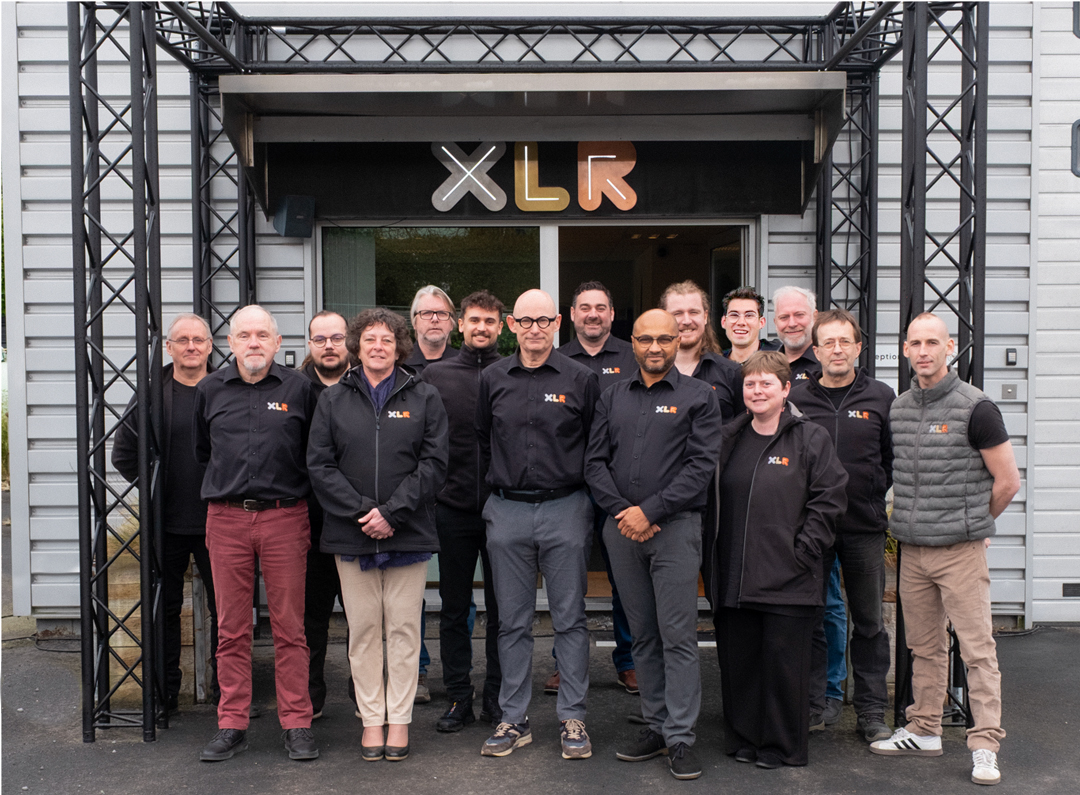
XLR is involved with new technologies such as immersive sound. And we want to develop the sector to its full potential. That’s why we’ve chosen TAF, L-Acoustics and Elation. XLR also offers a training and demonstration centre to familiarise customers with new technologies and help them come to grips with the products. The team now includes 16 people and continues to grow.
Historically known for its expertise in audio, the company has decided to expand its portfolio, first with lighting products, by adding a brand of structures with TAF, for which they have exclusive distribution in France and the Benelux countries.
Peter Van Velde, head of the division explains: “We need to be able to hang sound systems and lighting kits to respond to the requirements in the tender; hence, we needed a structure and rigging portfolio so that we didn’t have to go through other distributors. Given the growing demand, we decided to go direct with the TAF brand”.
.
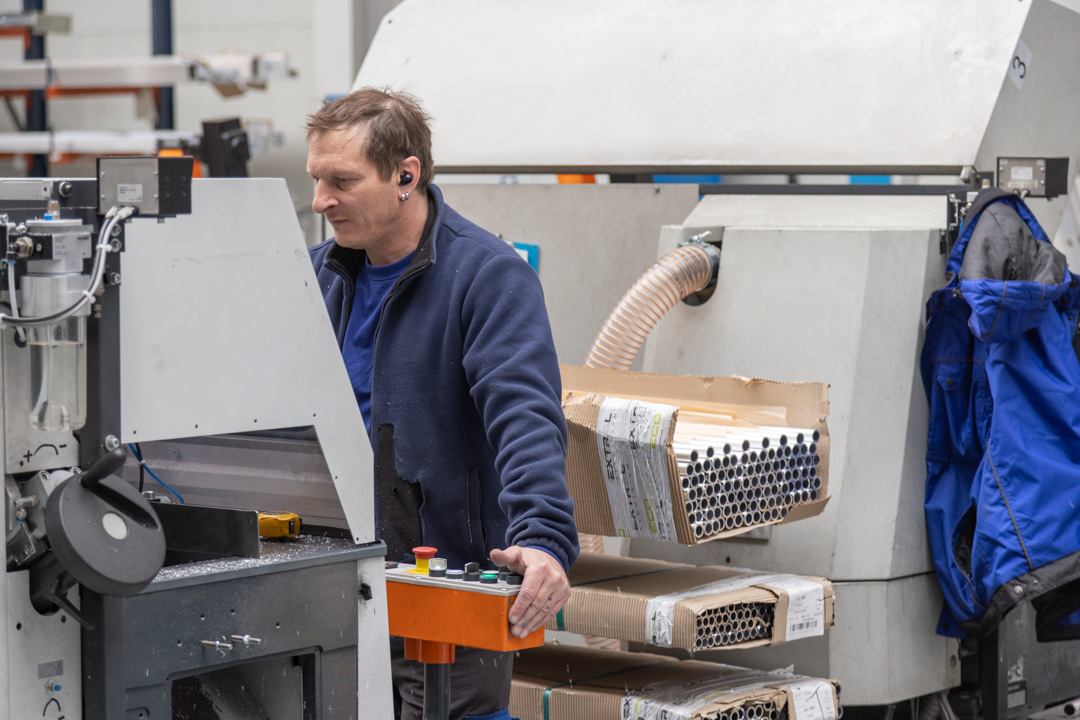
SLU: In terms of pricing, how are you positioned compared to your competitors?
Pieter Van Velde: Let’s just say that our customers, the dealers, are happy and that we are very well positioned. There are always more aggressive competitors in terms of price, but we have the advantage of having stock, and “Truss On Time” is also an important selling point when it comes to customer choice. Going through a distributor of another, cheaper brand can easily mean an extra eight weeks of lead time.
SLU: How did this partnership come about and how did you discover the brand?
Pieter Van Velde: I knew the company from before because they did a lot of OEM work. At the very start of my career – over 25 years ago when I was a disc jockey – my first trusses were already made by them, but under a different brand name. Then I worked for the same company as Milan Kolousek, but not at the same time. It was the biggest structure manufacturer in the world at the time. When Milan joined TAF, this connection enabled me to meet the founder Jaroslav Rosboril and then his son Jakub, who is now the general manager of TAF.
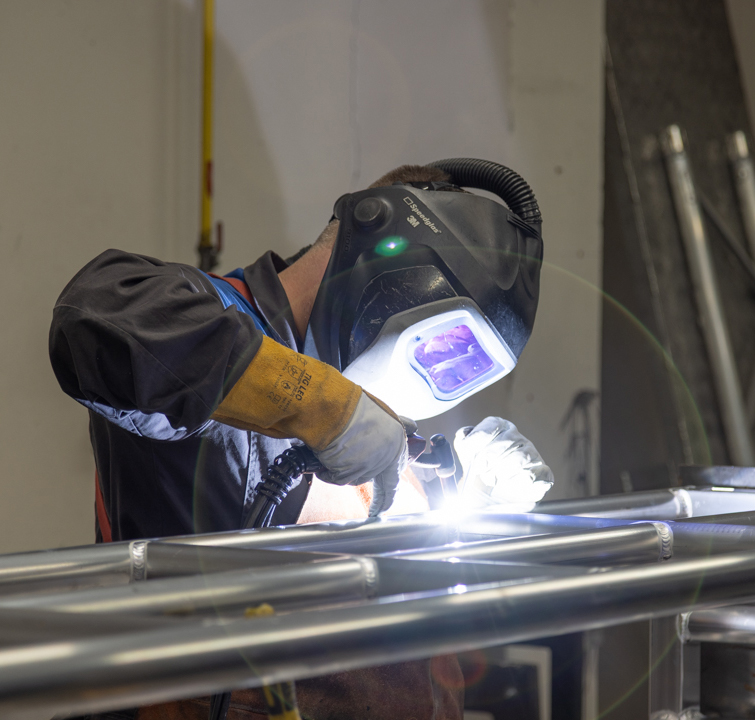
SLU: Have you already seen promising results from your partnership with TAF?
Pieter Van Velde: We haven’t done any major projects with them yet, but we have started to respond to some small calls for tenders. XLR is known for its audio systems, notably via the distribution of L-Acoustics. The trusses that have been put in place are mainly designed to suspend these large systems over stages 15, 20 or even 25 metres wide.
SLU: Are you the only structure specialist at XLR?
Pieter Van Velde: For the time being, yes, because it’s very specific knowledge that carries responsibility. The numbers are rising fast, as are the load ratings and structure lengths. You have to know how to distribute the loads, and some requests require larger sizes or categories of trussing. We can’t forget that, when we work with elements suspended above the public, lives are at stake, so we can’t cut corners on safety. It’s a discussion that needs to be held with the customer, and one that requires a thorough understanding.
.
TAF, a family history of tradition and innovation
Founded 27 years ago by Jaroslav Rozbořil – the father of Jakub Rozbořil, General Manager of TAF – the company has gradually evolved with its employees, some of whom have been with the company since the very beginning. Located in the Olomouc region from the start, it is currently located in a renovated industrial site. The team has always taken great care to maintain its working environment – one of the secrets to producing high-quality products, according to the founder.
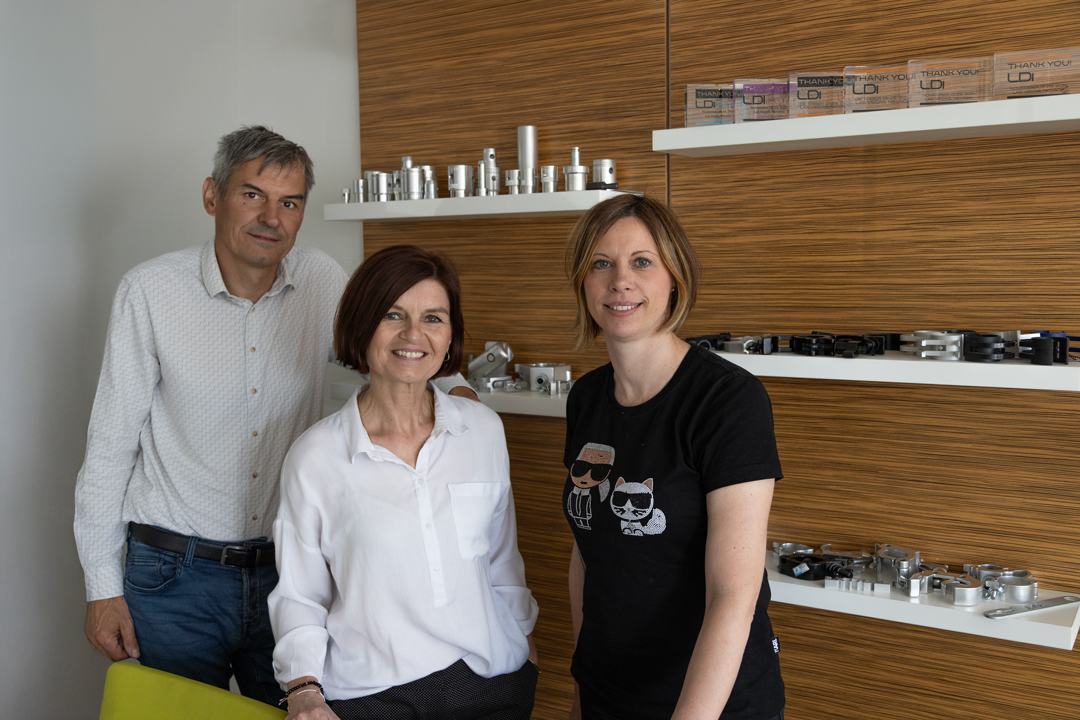
SLU: How many people are currently employed by TAF?
Markéta Šimková: There are four people in the technical department, four in the sales department, four people coordinating production, two in the purchasing department and two in marketing, plus human resources and reception.
With the manufacturing team, the managing director and the company boss, there are 120 of us in total. There are also teams in the offices in the United States and the United Kingdom. TAF is expanding and plans to increase the floor space of its administrative offices in the coming years.
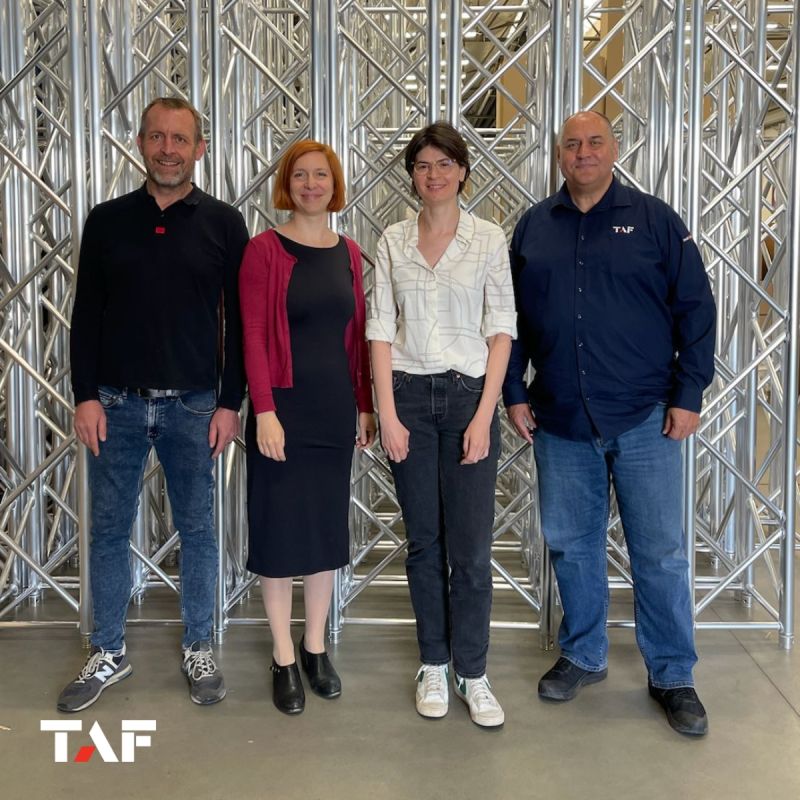
Born from 27 years of experience in OEM manufacturing, the TAF brand is now setting off boldly and with a clear ambition: to redefine the standards of the high-end structures by leveraging modern industrial production facilities, a team of engineers dedicated to custom-made solutions, and a well-organised international distribution strategy.
This evolution is not simply an extension of the company’s expertise, but the ongoing development of a brand in its own right that is gaining increasing market share, with a strong identity, a commitment to quality and a vision for the future.
Through solid partnerships, such as the one formed with XLR for France and the Benelux countries, TAF has established itself as a flexible, reliable and innovative response to the new challenges of events and staging.
More information on:
– The TAF website
– Their project blog
– XLR, the distributor for France and Benelux