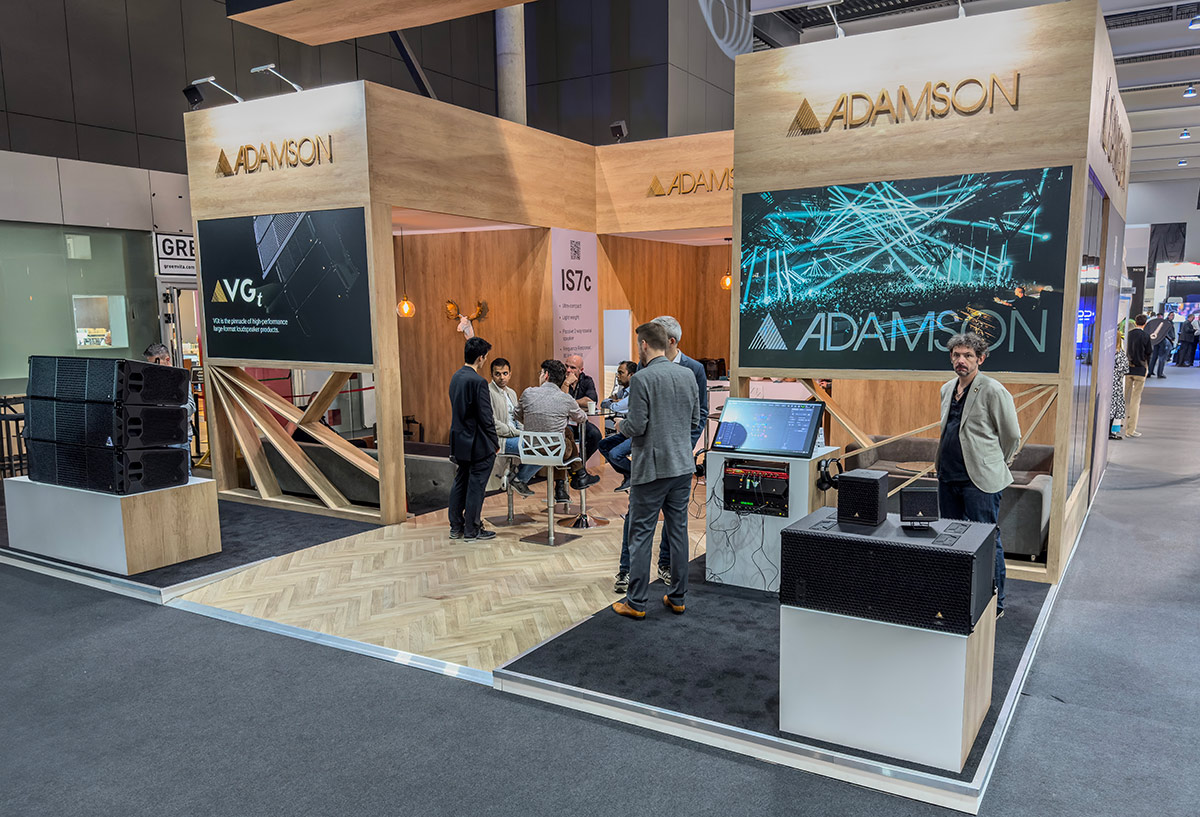
Unveiled shortly before ISE 2024, the new VGt system, the first model of the Vergence Group, fulfils Brock Adamson’s dream of having a large-format line array enclosure that is amplified, processed, supports Milan and incorporates virtually all the technology designed and built at his factory in Port Perry, Ontario.
Perhaps just the two 3″ drivers are still made in Italy. A few years have passed between the conception of the idea and its completion, allowing the Energia, or ‘E’, to develop. In the meanwhile, two important new features have appeared: a meticulous control of the bass dispersion, and the perfection of a 5.5″ Kevlar dome compression driver.
What has changed between E15 and VGt? Quite a lot. In fact, everything except the wood and the front grille. There’s a 5 kg difference between the new version and the so-called old version. This is a negligible weight gain, considering that the VGt has eight transducers, as opposed to six, in addition to five class D amplifiers and a switching power supply with a total peak output of 10 kW. It also has state-of-the-art processing, Milan stream support, AES70 control and analogue redundancy.
When one considers the weight of the multicore needed to connect the speakers to their amps, this difference disappears like a popsicle in the sun. Externally, VGt’s measurements are closer to E12 than E15, thanks to the new 13″ woofer. The 39 cm of the E15 has become 34 cm, which, with the same array length, means you can fit one more module every seven units.
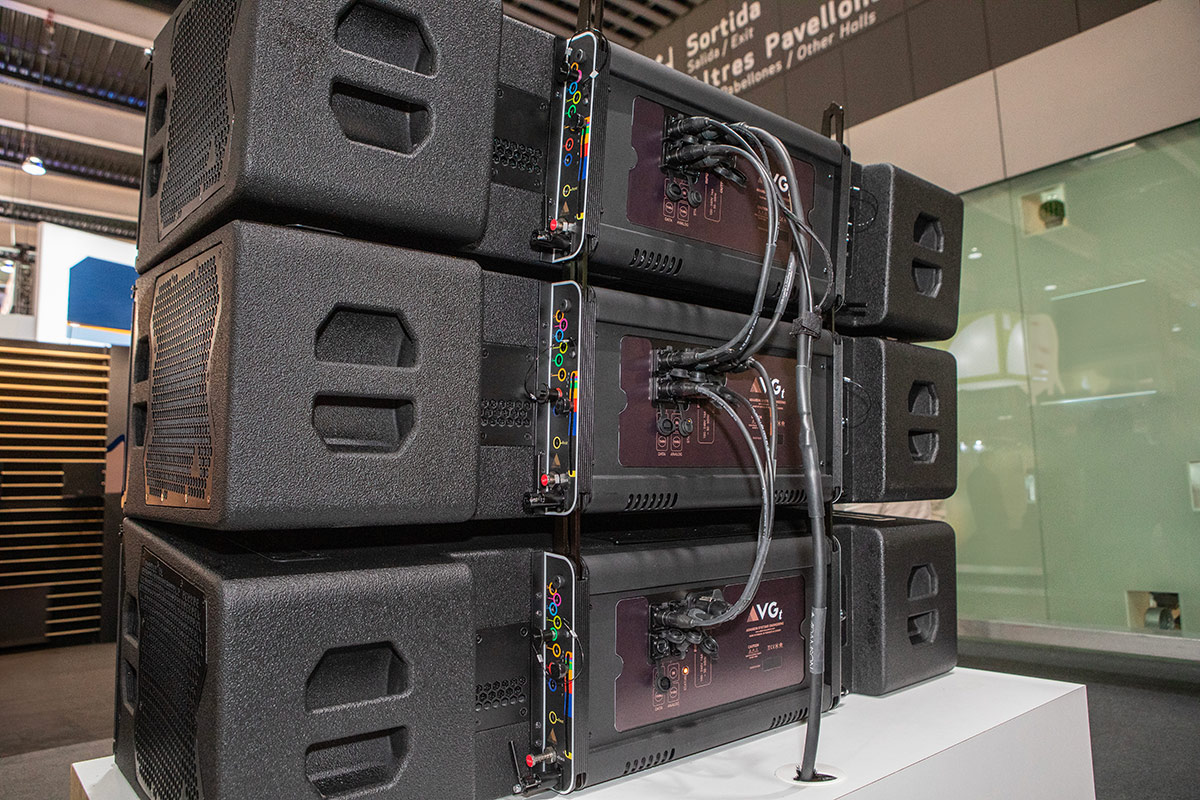
While we wait to get to listen to this newcomer (Guy, Didier… let us know, if you are reading), the real difference we can ascertain is in two values and a polar diagram. While the E15 could go down to 60 Hz at -3 dB with two 15″ speakers, the VGt delivers 50 Hz at -3 dB with its two new 13″ speakers, which are supplemented by a pair of 10″ speakers on the sides. As we’ll see later, the deeper bass is more effectively projected because it’s potentially cardioid.
Another major difference is that thanks in particular to its two new Kevlar drivers and two new 3″ HF compression drivers, VGt delivers 4 dB more than E15, reaching 151 dB SPL and taking the top spot among large-format line array modules, just one little decibel ahead of an American manufacturer from the East Coast, who managed to get 150 dB.
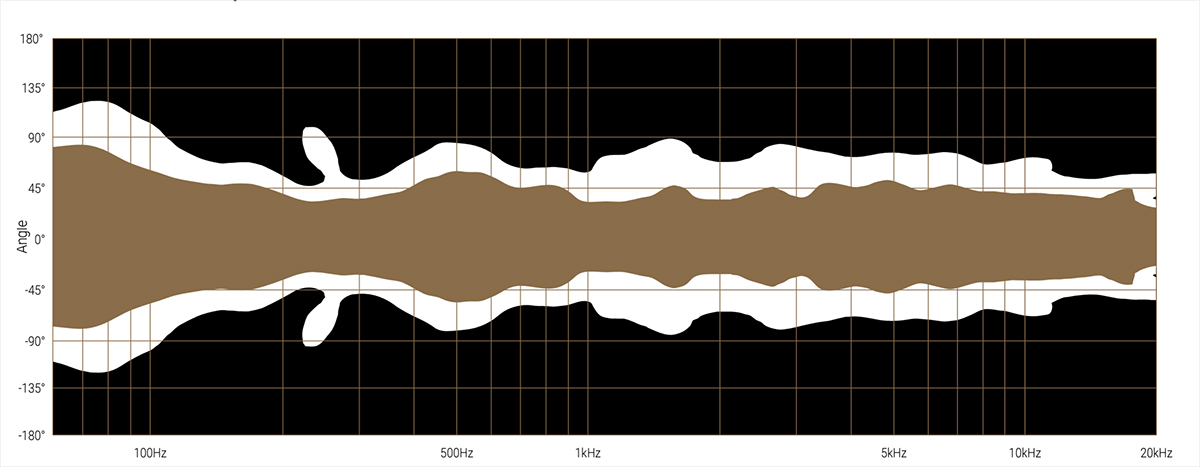
The horizontal dispersion reflects the pedigree of this enclosure, and it’s a strong one. Even the first octave (50-100 Hz) does not exceed 140° and quickly returns to the nominal 90°, except at the crossover frequency between the bass and the two drivers, where a little extra energy is noticeable. The rest is perfect and bodes well for a ‘large format’ range.
Having established this context, we now can turn to Mario Ahrberg, the Head of Applications EMEA, whom we had the pleasure of interviewing in Barcelona, for a few details about this new range, known as the Vergence Group, and its first model, the VGt.
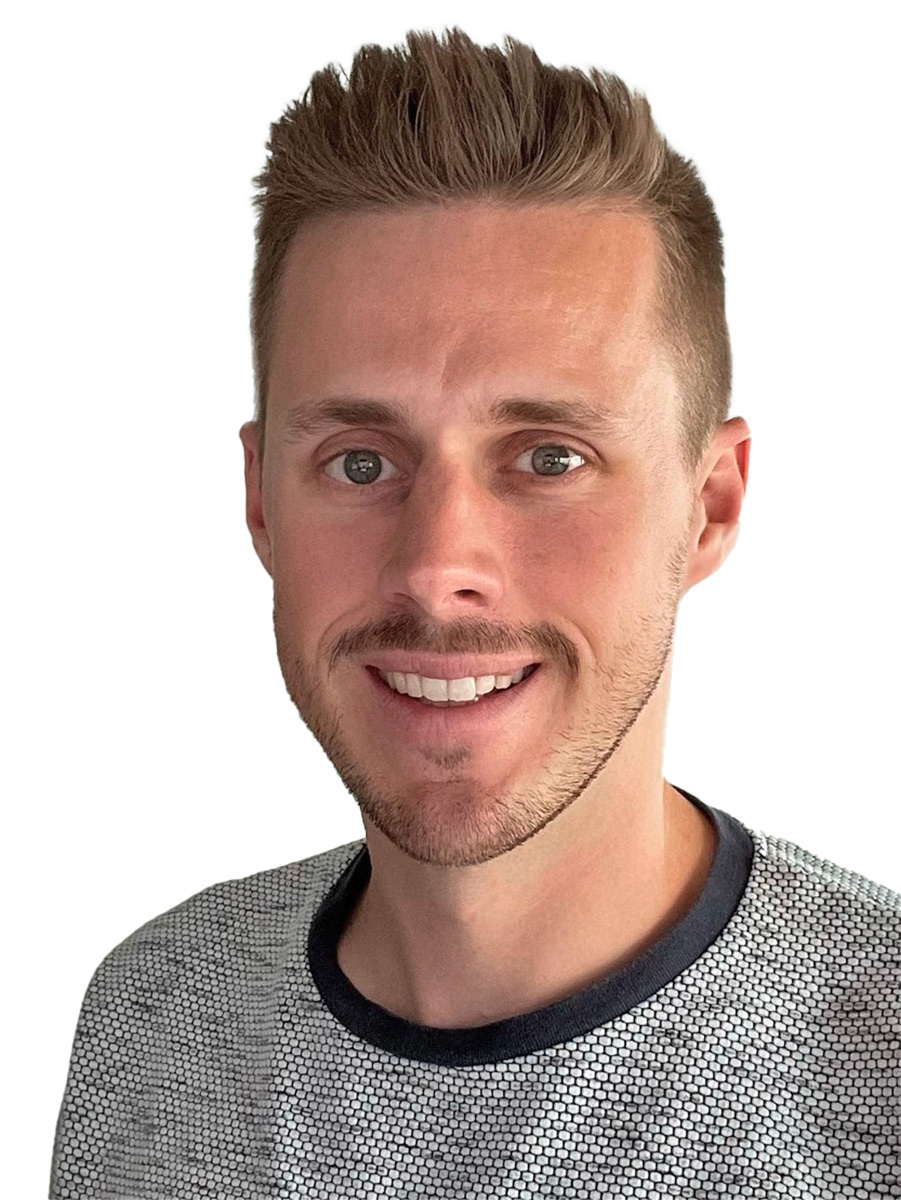
SLU : What size is the mid-range driver?
Mario Ahrberg : As the M140 reference indicates, this transducer has a diameter of 140 millimetres or 5.5″. It is an entirely new, patent-pending product that represents an ideal combination of driver and cone technology in the midrange band, where it is most needed. It doesn’t introduce any intermodulation distortion over the wide bandwidth in which it operates, from 300 Hz to 3 kHz, meaning that it covers almost the entire vocal range.
Above that range, a 3″ compression driver takes over, with a special phasing component to ensure the optimum horizontal dispersion, where if one driver opens a little too much, the other doesn’t open enough, so you mix the two to get what you’re looking for. The 3″ driver is optimised to deliver maximum performance at the top end of the spectrum.
SLU : In the E15 you were already using the principle of a mid-range cone supplemented at the top by drivers…
Mario Ahrberg : That’s right, there was a 7″ cone driver in a coaxial configuration with a 4″ compression driver. There were two in E15 and only one in E12. The advantage of the new system is that, while retaining the coaxial principle, we no longer need to traverse the diaphragm and… well, I can’t tell you any more about it, the patent is pending (laughs).
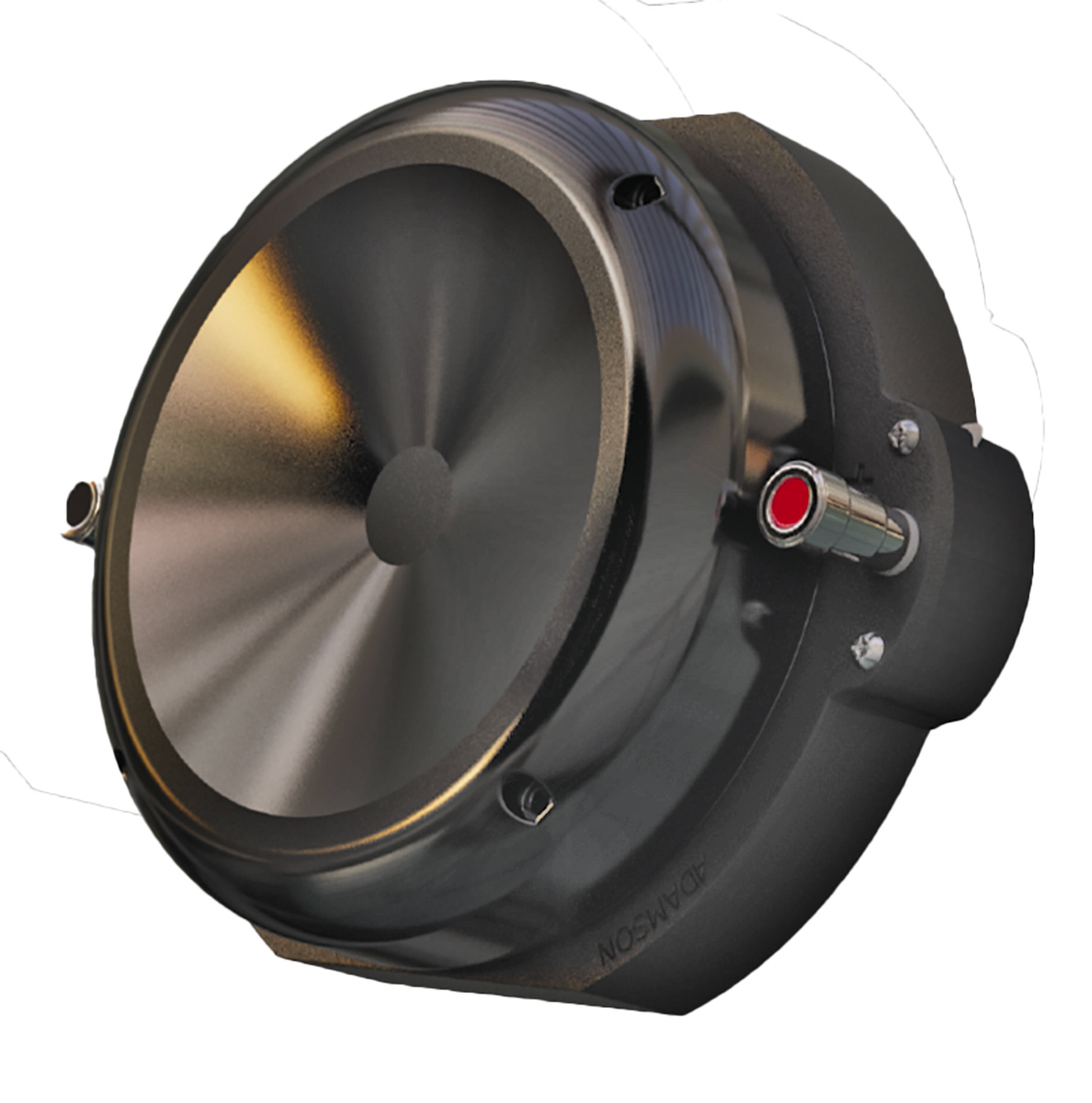
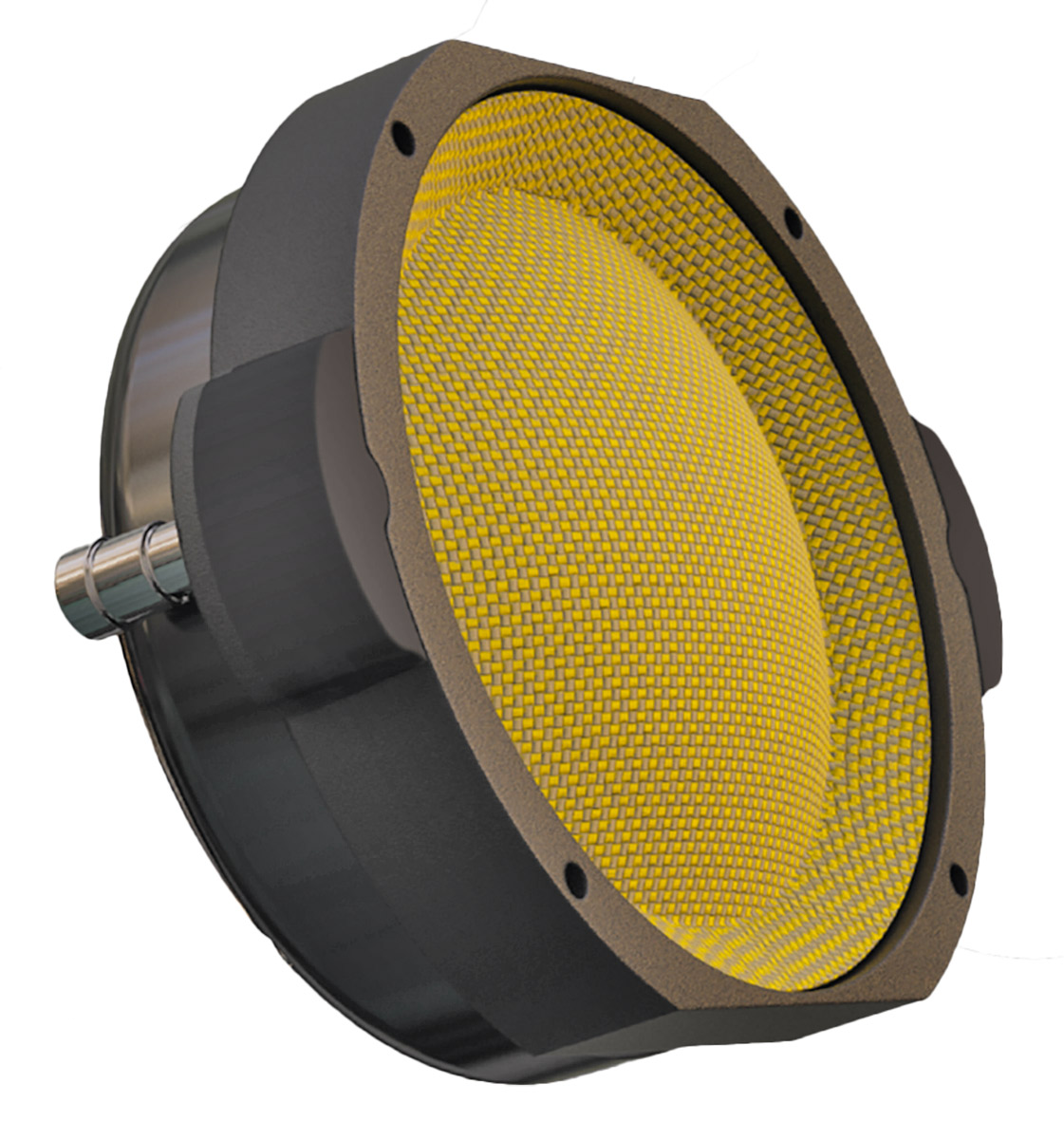
SLU : The image of the M140 doesn’t show any suspension
Mario Ahrberg : On the front, there is no type of suspension. The membrane, let’s say the Kevlar dome, is glued to the edge. There is a small silicone suspension between the coil and the magnet. This dome is exploited inside a compression chamber, so movements are minimal.
SLU : It doesn’t seem to have an opening to cool the coil. Doesn’t it heat up?
Mario Ahrberg : Yes, of course, but the M140 is a closed load and the heating is, like the excursion, minimal. Heat dissipates naturally through the metal body. There is no loss through thermal compression. Its sensitivity is amazing!
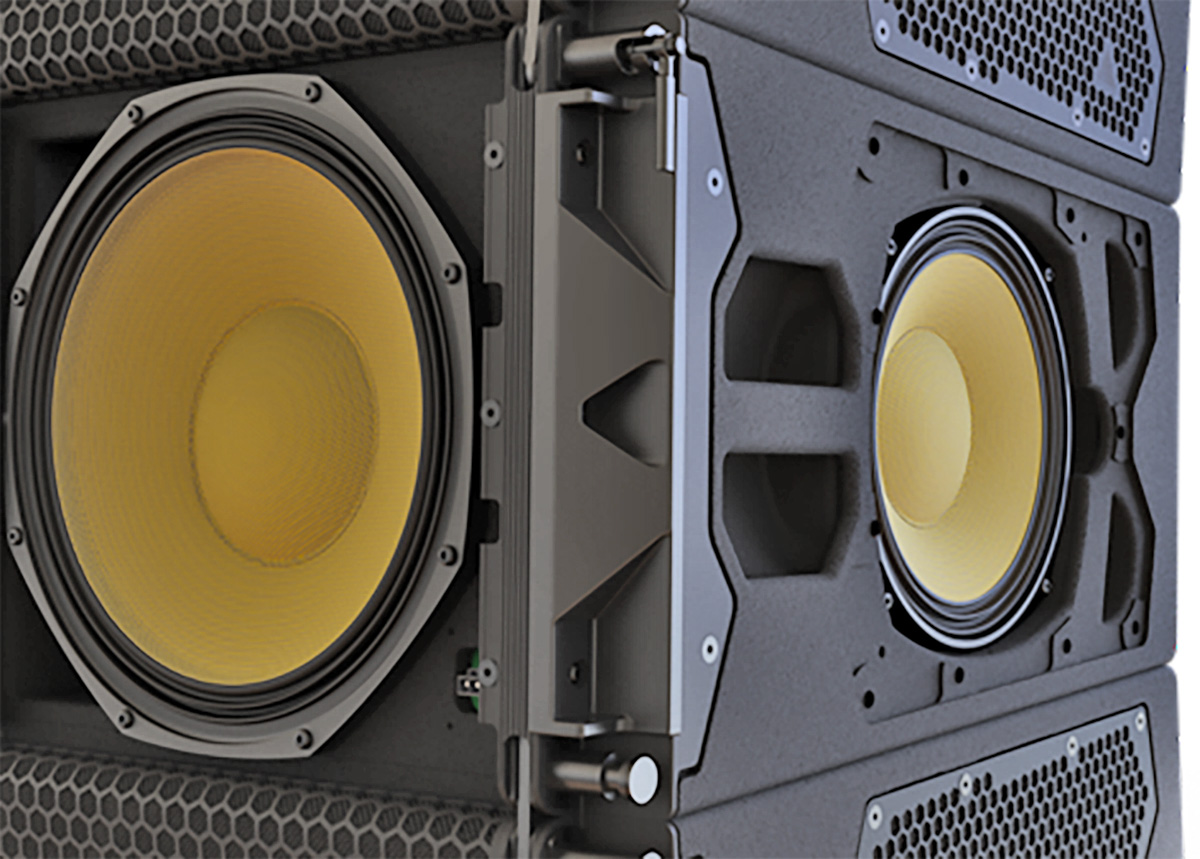
SLU : The amplifier section includes five independent modules…
Mario Ahrberg : One for each 13″, one for both 10″, one for both mid-range drivers and one for both HF drivers.
SLU : Why did you adopt the 13″ format for VGt?
Mario Ahrberg : Very simple. The reason is the height necessary to generate a nice wave front of 6° vertical and the height of a 13″ is exactly what we need. What’s more, with two 13″ and two 10″ speakers we can achieve the same results as with two 15″ speakers, not to mention the transition to a cardioid pattern. Finally, we gain in efficiency because, with the same size of array, we’re more powerful. Much more powerful.
SLU : Does the type of bass generated by this enclosure combine better with the subs?
Mario Ahrberg : Of course. We’ve done everything we can to deliver the best transient response in VGt and the use of the 13″ is part of that. We’ve used our curved Kevlar cones again in the same way to be more effective at the top end of their useful spectrum while retaining the greatest ability to move air.
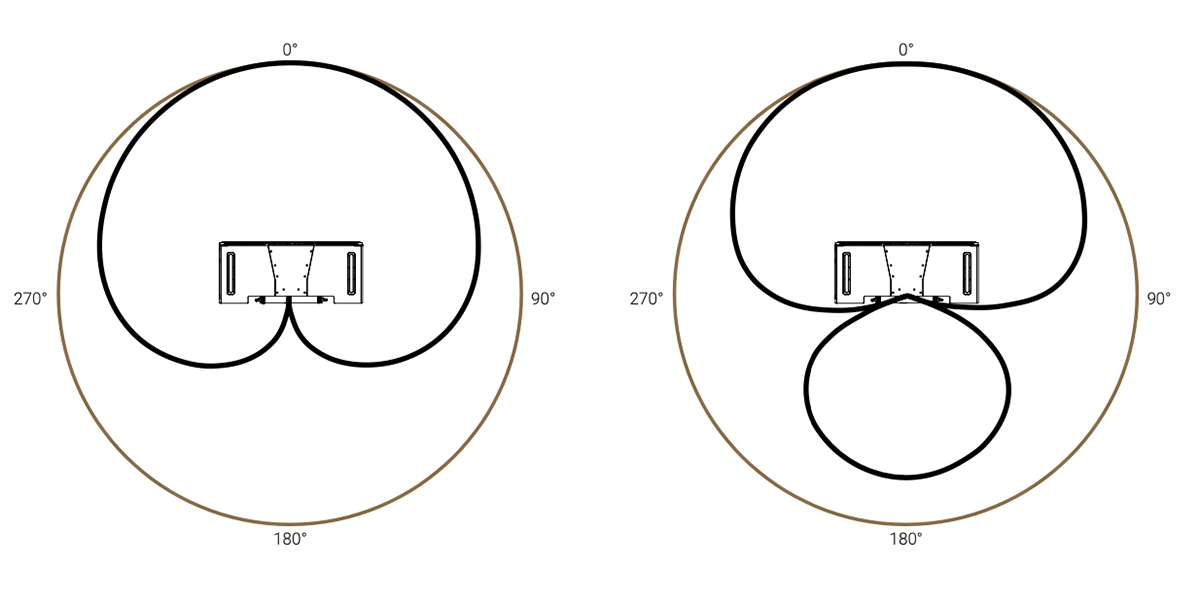
SLU : You’ve introduced three directivity modes: omni, cardioid and hypercardioid. Since we’re talking about presets, will this change in the future with an update?
Mario Ahrberg : No. We’re going to stick with these three choices. It’s a very complex system to programme and we don’t want to open the door to even the slightest modifications. We can’t see what the advantages might be. With cardioid, we clean up the rear but keep a bit of pressure on stage and on the sides. With hypercardioid, you concentrate on the front but generate a lobe on axis at the rear. Finally, in omni, the 10″ contributes in phase with the 13″, bringing a little more level to the front.
SLU : How do you feed the enclosures with… everything?
Mario Ahrberg : There are six connectors on the back of each one. Three inputs and three outputs. One input for the network, one for the analogue signal and one for the mains. And the same number of outputs. For the mains, as for the other two connections, you go into the first box and link it through to the next two; and so on, three by three.
We’ve chosen to limit the mains and analogue to three units, to make wiring easier, bearing in mind that we’re on 16 A mains. Three units draw the same current as a PLM 20K44, which also drives three E15s, but we output 4 dB more, so we’re much more efficient. Of course we’ve improved the sensitivity of the transducers, but our amps are also more efficient, and we don’t have the loss associated with cables. Inside the cabinets they are no longer than 40 cm…
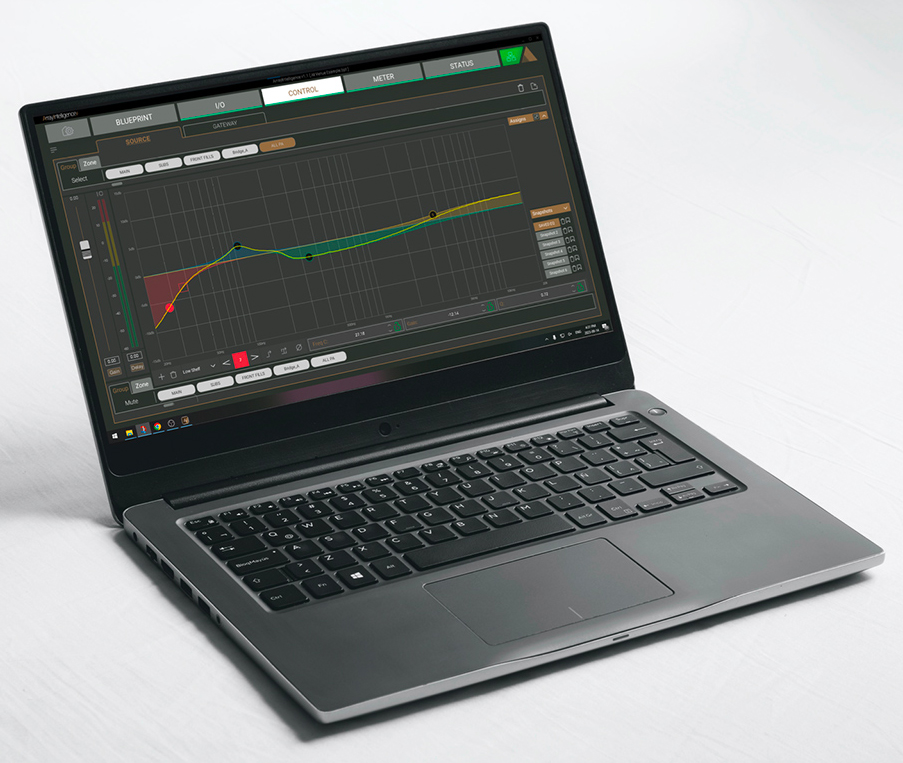
SLU : With amplification and processing for each unit, you have a great deal of freedom of adjustment, not just in terms of timbre…
Mario Ahrberg : Yes, that’s one of the big advantages. We have an Arrayintelligence optimisation tool that automatically creates FIR filters for the individual enclosures. The advantage is that, since we already provide FIR filters on the outputs, we can add them together and optimise without generating additional latency. On every other system I know of, this is not the case.
SLU : How close is the VGt series to completion and availability?
Mario Ahrberg : We’re currently working on the presets. The electronics and transducers are fine, with perhaps a few minor details to be worked out before we go into full production, but nothing major (smiling). We’re in the final testing phase. We’re going to start taking orders at the end of 2024, but there’s a French company that’s very active with Adamson and… (OK, we get it, Mario. Didier, we’re counting on you!)
SLU : The question on everyone’s mind: why “Vergence” and what do we mean by “Group”?
Mario Ahrberg : Divergence, convergence, that’s the sound, so we’ve kept Vergence; we’ve kept Group because it’s going to be a group of products, and there are new things to come.
SLU : A sub, perhaps?
Mario Ahrberg : It’s called Vergence Group, and it won’t just be VGt. Just bear with us.
For further information: Vergence Group and the VGt