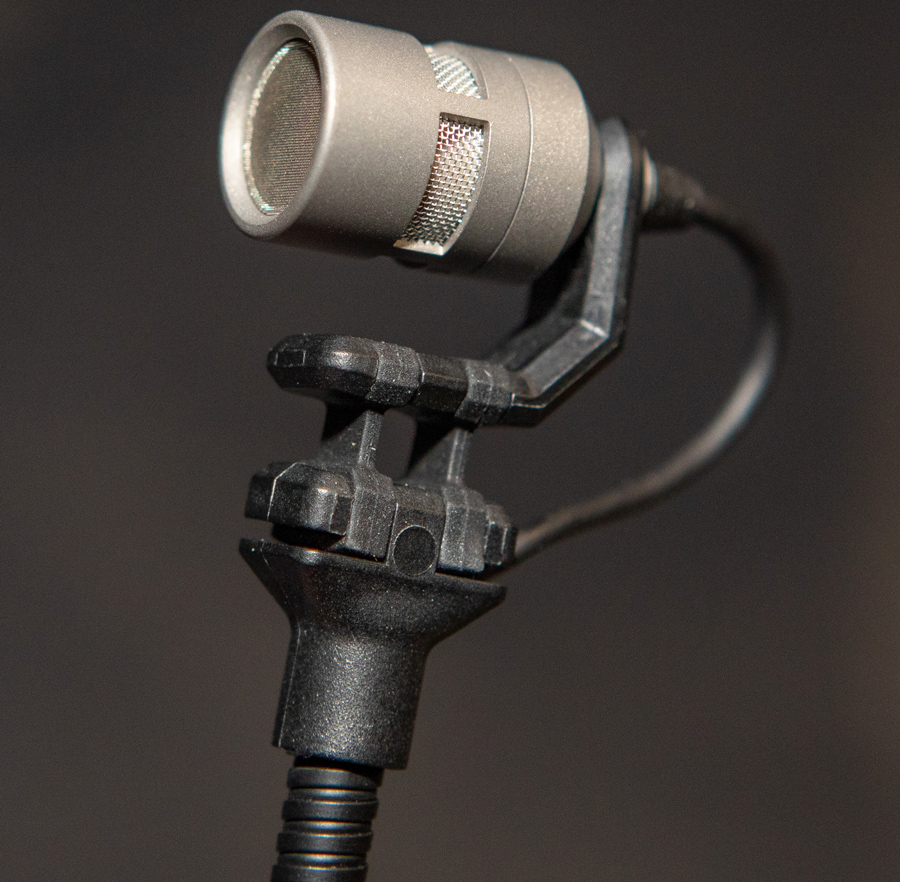
Though we are going through the most uncertain of times, and our morale may be on a roller-coaster ride, Neumann’s R&D is giving us a great 2022 surprise, and it may be that a star is born – sorry, dass ein Stern geboren wurde.
After years of work – six, we’re told – the venerable German brand has just unveiled the MCM, a microphone system that is going to do a lot of good for our ears and for the Neumann brand, which seemed to be resting on its laurels, or even lapsing, with their digital range.
Together with its comprehensive set of accessories, the Miniature Clip Mic System or MCM was presented to us at the Pin Galant, in Mérignac near Bordeaux in France, with the help of OdinO, an orchestra that nicely combines classical and pop music, featuring six violins, two violas, two cellos, two contrabasses, as well as brass instruments, a piano, an electric guitar, electronic drums, and more. It was a dream come true for testing out an instrument microphone.
A big “Thank You” to all the musicians and to the conductor of OdinO, Sylvain Audinovski, but also to the teams of the Pin Galant and to Laurent Balutet, the general manager, for their collaboration and hospitality.
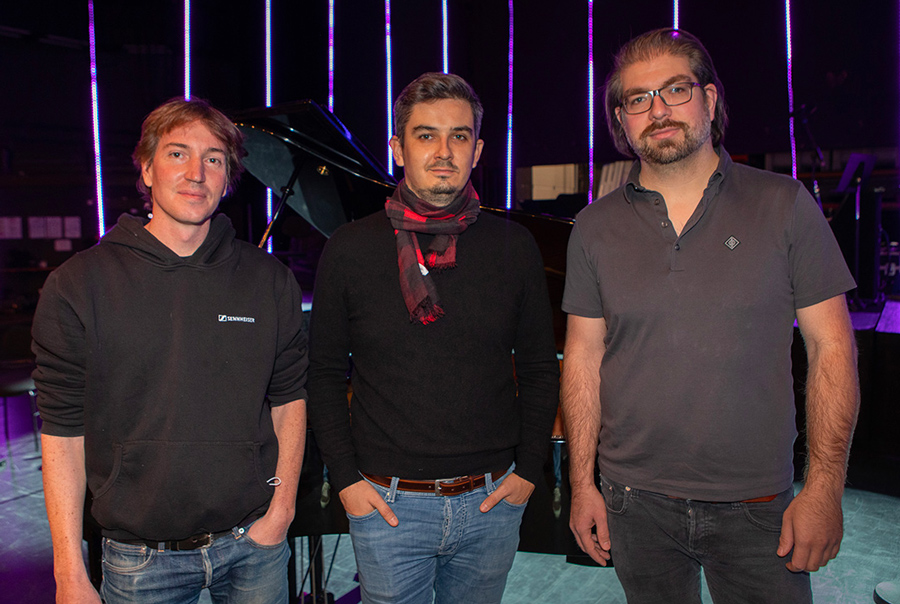
We were able to see, touch and, above all, listen to this new transducer, and all the better because accompanying OdinO on tour was Espace Concept, from Besançon, with Alain Roy, a true microphones heroe at FoH.
Also on hand were: Charly Fourcade, Custom Development & Application Engineer at Sennheiser; Hadrien Soulimant, Pro Audio Business Development Manager at Sennheiser and Neumann; and particularly Stephan Mauer, Portfolio Manager of products dedicated to live and broadcast applications at Neumann.
The latter arrived with a trunk full of transducers, goosenecks and mounting accessories. We asked him a few questions.
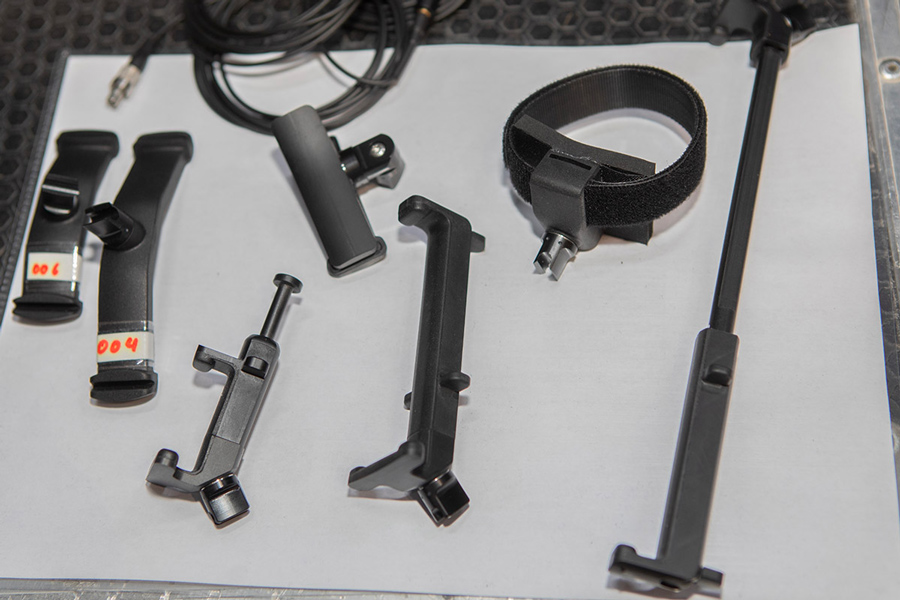
SLU : The range of accessories looks pretty extensive…
Stephan Mauer : We did our best to make sure that the MCM can be mounted on virtually any instrument. So there are nine mounting clips, all capable of clamping the gooseneck using a groove that rotates in 90° increments.
Some of them will be very slightly modified between now and the final release of the MCM system in the spring of 2022, but their number, shape and functionality have all been finalized.
SLU : The trick is having separated the transducer, gooseneck and output cable…
Stephan Mauer : Yes, the capsule can be unscrewed from the gooseneck and this is important, as it represents the principal investment. It will be easy to change one of the other two parts in the event of wear or breakage. It will also be possible in the future to change the pickup pattern by screwing on a new capsule.
SLU : For the time being, it’s a cardioid?
Stephan Mauer : Yes, but should we develop a hypercardioid or an omni, the investment will be smaller because you won’t have to buy everything again. We tested a hypercardioid but a cardioid polar pattern turns out to be the most natural sounding, and it provides the most effective rejection on stage.
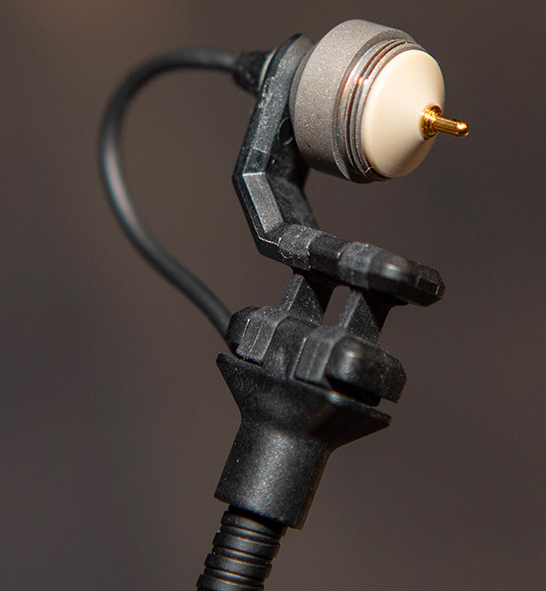
SLU : The KK14, a completely new capsule…
Stephan Mauer : Absolutely. It’s all new: the type of microphone, the technology of this capsule… for us it is a major step forward in the world of live performance.
Getting back to our capsule, it has the electronics as close to the diaphragm as possible and the body is made of polished titanium, which makes it robust, light and non-reflective.
Its equivalent noise level is extremely low (23 dB A-weighted), while the maximum applicable SPL is 152 dB, which means that it is quite capable of capturing the softest as well as the loudest sounds.
A single capsule covers the full range of dynamics required on stage, without any compromise in terms of noise or distortion.
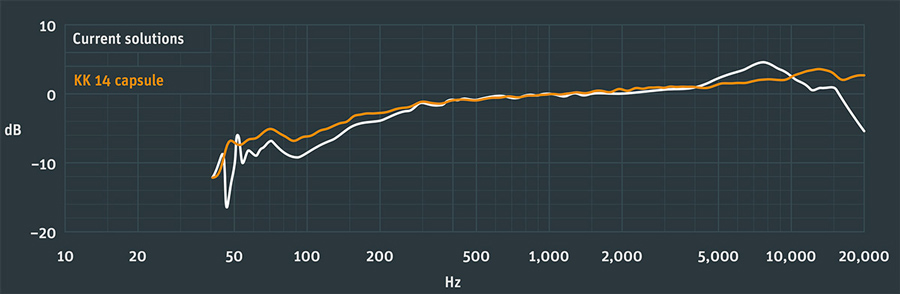
SLU : The output lead of the microphone is connected to the back of the gooseneck…
Stephan Mauer : And this connection has been successfully tested through more than 3000 cycles, which is equivalent to five years of regular use. On the other hand, since it is a jack type plug, it is possible to rotate it to unravel loops or twists in the wire without disconnecting it, which is convenient.
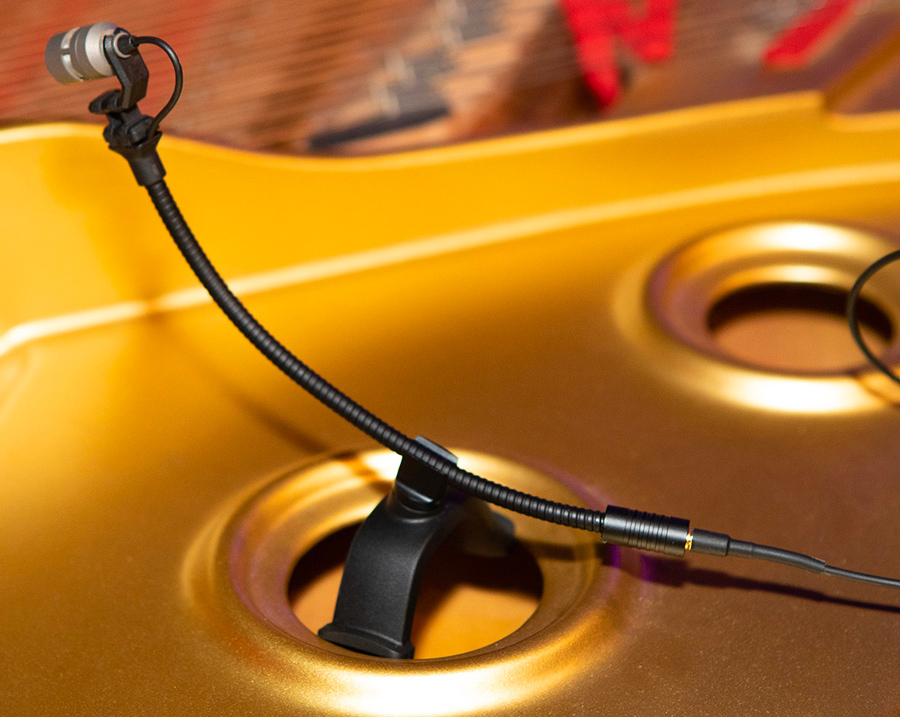
SLU : This “extra” connection might scare some people.
Stephan Mauer : We have thought about that and a specific accessory has been designed to lock the two pieces together. We are thinking of delivering it with each cable or with each gooseneck.
The contact is nevertheless solid and the plug holds very tightly, while allowing for it to be jerked out without damage, just in case (he smiles). The choice is left up to each technician.
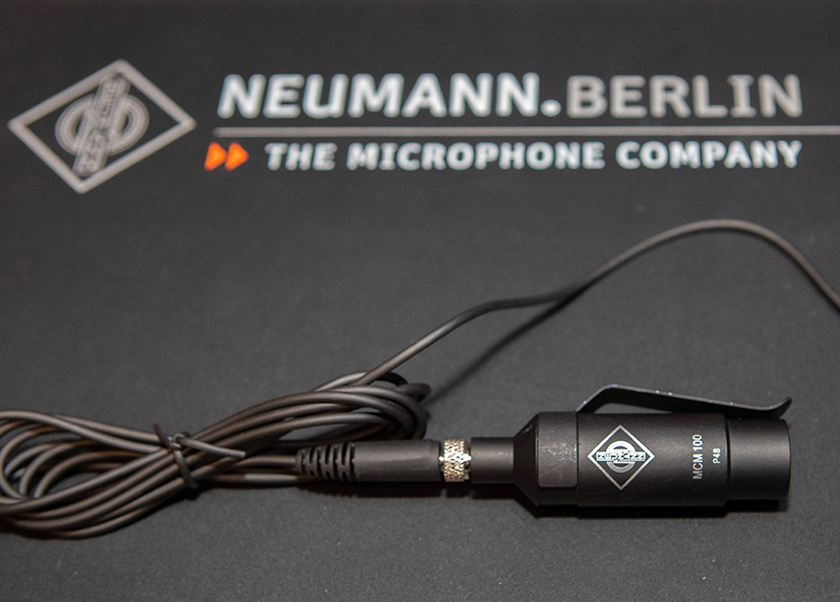
SLU : How many types of cables are there?
Stephan Mauer : There are four, in order to cover any requirement: LEMO, MicroDot, Mini-XLR4 and 3.5 mm stereo jack, the latter connecting to the MCM100, the XLR output adaptor. The one you see is a pre-production model, the final one will be slightly different.
SLU : So they are all available as separate components, but packages are also planned?
Stephan Mauer : Yes. There are eight in all, including one with a set of two microphones for the piano. They are designed specifically for each instrument and include everything except the output cable to the transmitter pack. It could make economic sense to get a number of them and then supplement with targeted purchases. There is only one color available, black for the accessories and the cable, and the microphone is dark grey.
SLU : Have you done testing for each instrument?
Stephan Mauer : Of course we have, but this is the first time we will hear it on a classical orchestra of this size live. This will allow us to further optimize its sonic characteristics to give it the highest versatility and ability to pick up everything with the least possible use of electronics and processing.
SLU : Let’s go back to the origin of this stage microphone system – this is your first electret capsule.
Stephan Mauer : Yes. This completely new capsule is the work of Neumann’s R&D. We became part of Sennheiser in 1991, but we retained our design department. When we started working on it, we quickly realized that, for obvious reasons of compatibility with transmitters that only supply 13 volts, condenser technology would be impossible. But we had to create the best possible electret transducer and give it a high level of consistency in its performance.
This transducer is mechanically similar to the KK184 which equips the 180 range, and is handmade in Germany in the special Neumann production at Sennheiser, like all the other Neumann microphones. The high manufacturing quality allows us to tighten the tolerances in terms of the sensitivity and the frequency response, defects that many users have noticed on other electret products. All MCM units sound the same.
SLU : Are there advantages that caused you to choose to make it not as small as others?
Stephan Mauer : Of course there are! The size of the transducer influences its directivity and performance. We tested 6 mm and 8 mm diameter capsules but opted for a larger size to get a better bottom end and a more uniform and slightly wider pickup pattern over the whole spectrum to avoid cutting off too much of the environment and deliver a more natural, rich and pleasant sound.
Finally, the microphone’s self-noise or equivalent noise is correlated to the size of the golden part of the diaphragm, so the larger the diaphragm, the less noise. It is thanks to this choice that we are able to achieve 23 dBA of intrinsic noise with a maximum SPL of 152 dB!
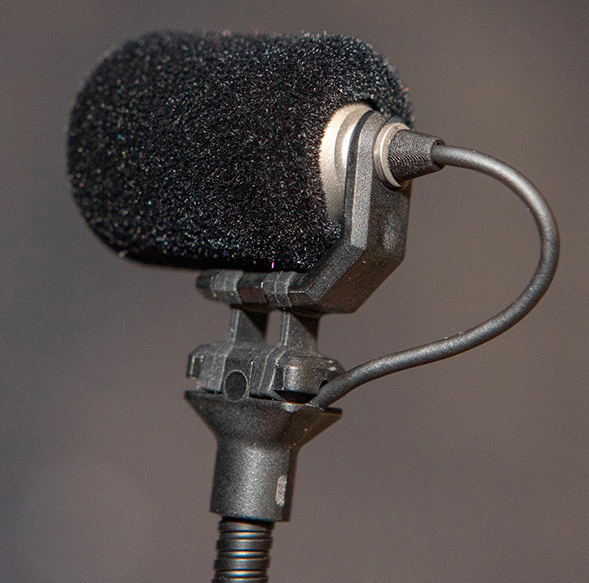
SLU : What about the windscreen…
Stephan Mauer : It comes in the kits as well as individually, just like every other component of the MCM system. We spent quite a bit of time working with a miniature wind tunnel to determine the size, material and shape to make it unobtrusive and effective. You only lose a tiny bit of the extreme high end when it is used.
SLU : How do you isolate the transducer from the instrument on which it is mounted?
Stephan Mauer : In three ways: first, each clamp has a rubber strip to protect the instrument and to provide a primary isolation against the transmission of vibrations; second, the microphone is isolated by two elastic legs at the top of the gooseneck. Finally, the output wire of the transducer forms a loop.
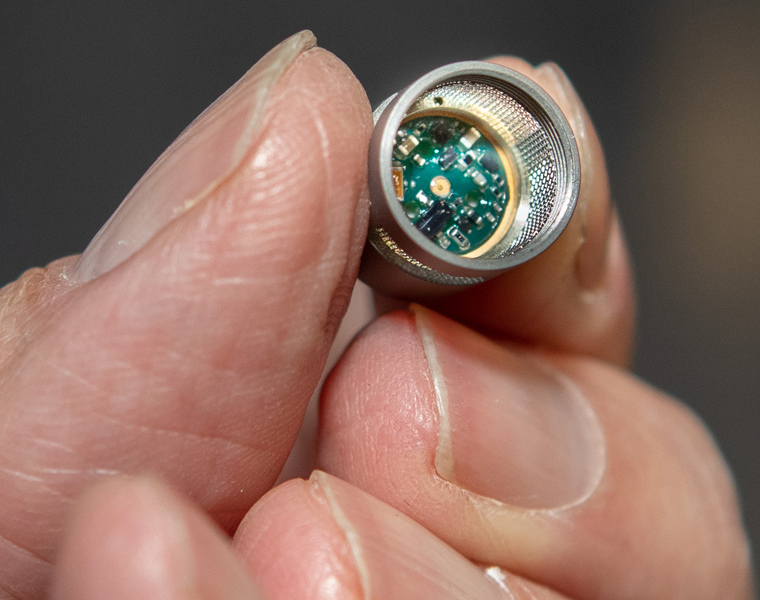
SLU : Now that you have a new electret capsule, are you going to offer it in other product lines, like a more affordable handheld microphone…
Stephan Mauer : It’s an idea, yes. I think it could also be used on a headset at the end of a mini-gooseneck for sports commentary!
Listening
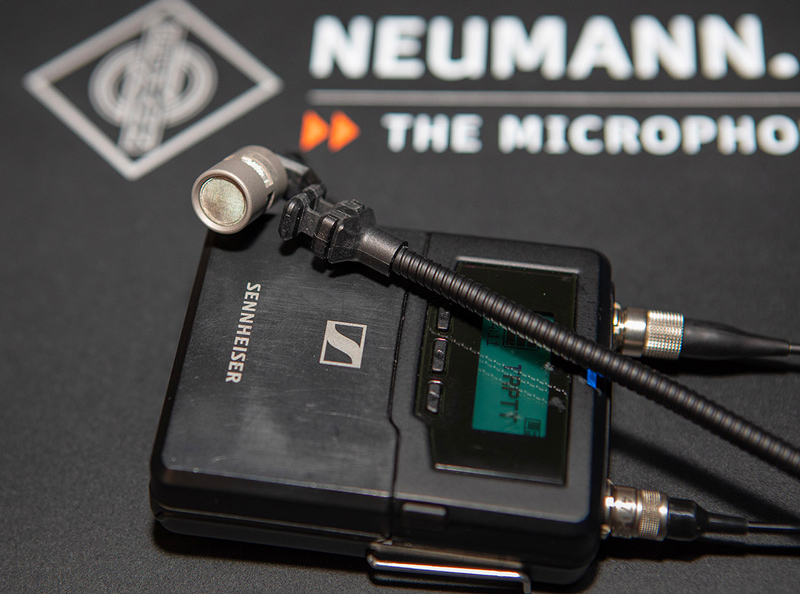
The MCMs were attached to all the strings and brass in place of the supercardioid mics usually used on the tour, and the gain settings of the Sennheiser 6000 and 9000 digital transmitter packs were carefully adjusted according to Alain’s requirements.
Let’s specify from the outset that Alain mixes in a very respectful way, using optimal transducer placement, gain levels that best isolate the source from the other instruments and the room, as little equalization as possible – or even none at all – and finally, in order to preserve the phase, no low cut. Contrary to what one might imagine, the feedback rejection is better and the sound is much fuller and more faithful.
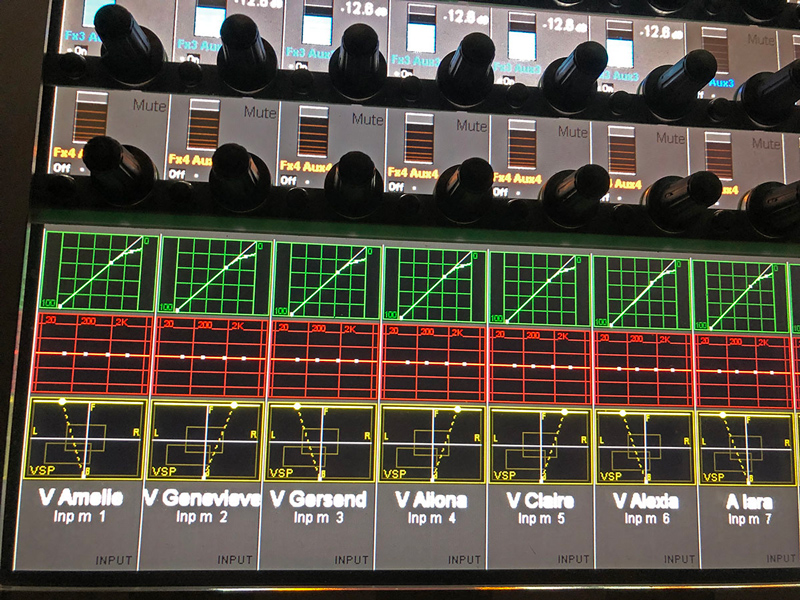
Following the same approach, after having listened to the L-Acoustics dV-Dosc and SB18 system, and the central Kiva array at the Pin Galant, Alain asked that the central array be brought down a little, in order to assess the contribution of the front and lateral fills and, above all, to ease the equalization applied in the L-Acoustics universe and in the Meyer Sound matrix at the front end, which also has DSP resources.
From the very first notes, we are struck by the fullness of the strings and their number. A mute on Alain’s console removes some tracks that – enhance – the performance of the orchestra during certain pieces. The result is even better. The sound is open, natural, relaxed and, at the same time, massive.
We don’t get the impression at all that we are listening to a strict close miking, which is nevertheless the case. We look around for a stereo pair. Each desk in the string section is also well isolated with its own texture and can be worked on without any problem. The same is true for the brass, which has all the necessary attributes except for the aggressiveness.
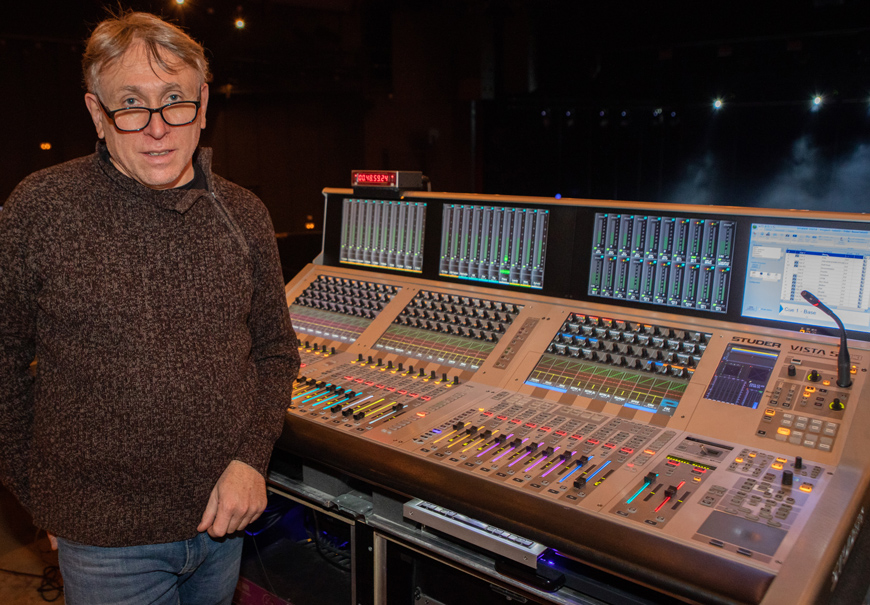
Noticing my astonishment, Alain once again suggests that I check that his console has only one EQ point on the master, none on the microphone channels handling the inputs from the MCMs; there is no low cut and a single compressor per microphone set with a very high threshold.
And it sounds great. The choirs emerge. The string players bring the violins up to their faces and sing a few bars into the instrument mic, one of OdinO’s many cool sonic performance innovations. This works, too, and it’s very nice.
So of course, a single listening in an empty and rather reverberant room (we were only present for the sound check) with a system that – although well maintained and in perfect condition – has become a rarity, is not enough. We will have to wait to encounter the MCM again to have confirmation, but it leaves us with a positive impression that is further corroborated by Alain who, while carefully minding his words, also liked what he had under his fingers and in his ears: “It’s clean, very clean, cleaner and smoother than we’re used to, with a very noticeable amount of room before feedback”.
However, there is still work to be done on the prototype accessories, some of which were actually produced by a 3D printer. The ball-and-socket joint of the part that couples the clamp to the gooseneck and allows it to rotate is not yet firm enough.
This means that the gooseneck could rotate due to sudden movements by the musician and misalign the capsule. Stephan Mauer has reported this and this defect will be corrected on the production components, which will be available in the spring of 2022.
The good news is that the prices will be reasonable and competitive with other instrument mics, with the major advantage of allowing the addition or replacement of only worn or defective components, thus keeping your inventory in perfect condition at a lower cost.
Finally, we’d also like to thank Ann Vermont, Communications Manager for Europe at Sennheiser, for inviting us to this experience at the Pin Galant and for joining us there!
Technical characteristics of the MCM transducer
Acoustical operating principle: Pressure gradient transducer
Directional Pattern: Cardioid
Frequency Range: 20 Hz … 20 kHz
Sensitivity at 1 kHz into 1 kohms: 3.5 mV/Pa +/- 2 dB (2.8 – 4.4 mV/Pa)
Rated Impedance: 50 ohms
Rated load impedance: 1 kohms
Signal-to-noise ratio, CCIR (rel. 94 dB SPL): 63 dB
Signal-to-noise ratio, A-weighted. (rel. 94 dB SPL): 71 dB
Equivalent noise level, CCIR (peak): 31 dB
Equivalent noise level, A-weighted: 23 dB
Max. SPL = 153 dB
More information on the Neumann website