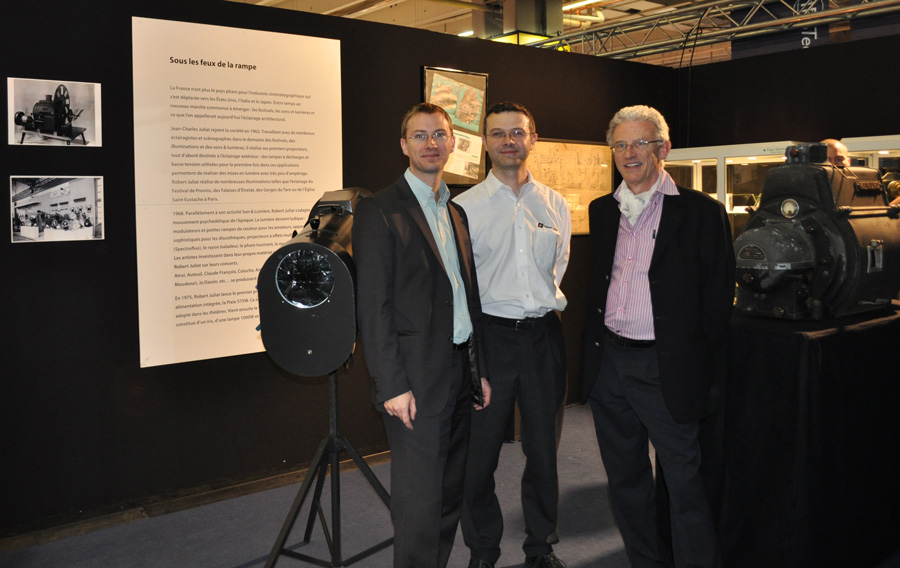
Located on the edge of the region of Picardy, the family business, Robert Juliat has made an art of combining the precision of a craftsman with the near insanity of new technology.
François and Frédéric Juliat, General Managers of Robert Juliat, welcomed us with open arms in Fresnoy-en-Thelle at the heart of their factory to see their museum devoted to the history of luminaires and share their views on the future of lighting.
Interviewing an Empire
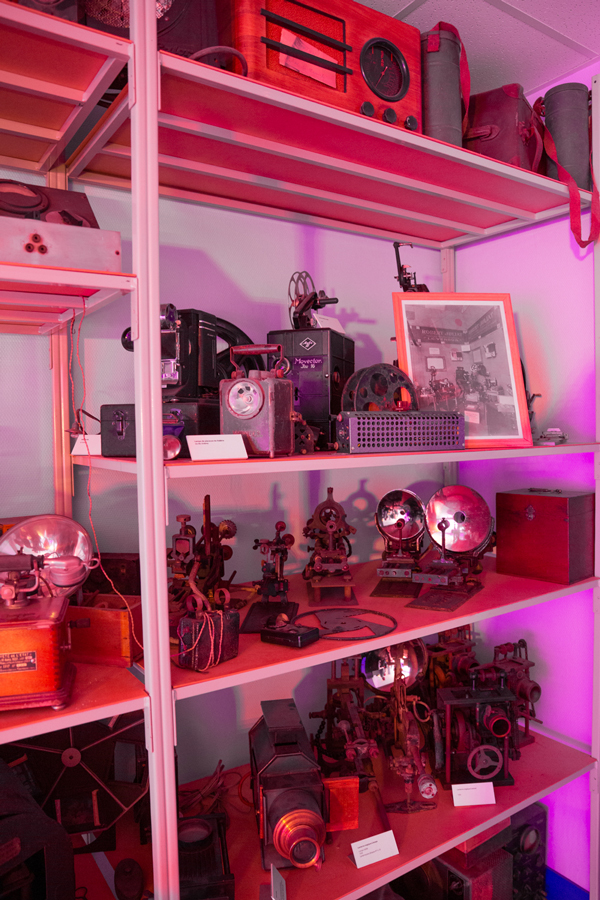
It’s quickly noticeable that, after close to 100 years, the family business hasn’t changed very much.
Robert Juliat, one of the pioneers of live shows, has been able to keep its family heritage and independence, with their leitmotiv summed up by the sentence: “creating solutions for lighting designers, technically sound, and surprisingly simple”.
In four generations, from Jean to Robert, then Jean-Charles to François and Frédéric Juliat, they have built an empire that can’t be missed. Jean, 120 years ago, worked with Melies as a projectionist during the beginning of film-making. Hence, becoming one of the first lighting engineers, he had to master the magic of electricity.
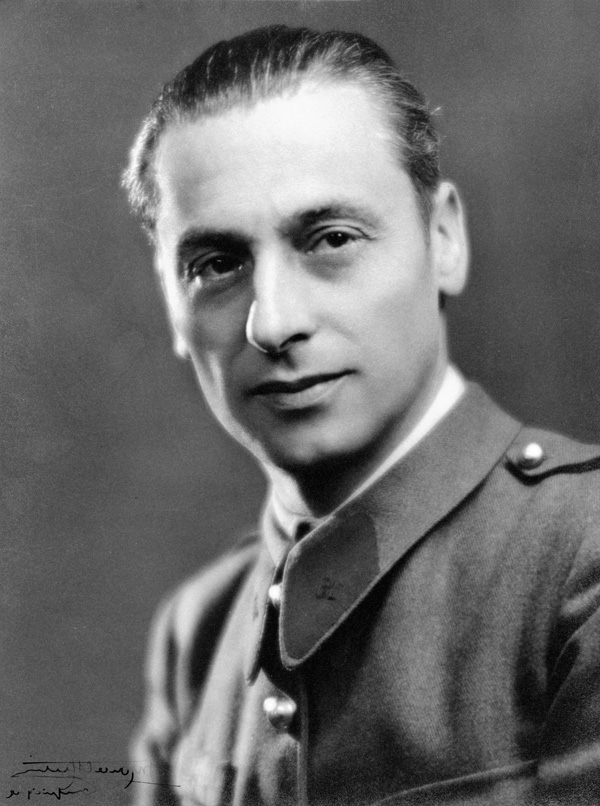
He passed on his enthusiasm to his son Robert, opening one of the first post-war movie equipment workshops in 1919, on Rue Trévise in Paris. They made some of the first single-lens luminaires used to highlight the entertainers performing on stage, during intermissions, while the projectionist changed the film reels. Robert Juliat was becoming a legend at the early age of 25 years old.

Jean-Charles, Jean’s grandson, who was already a skilled technician, boarded the family boat in the ’60s. Theaters and movie theatres were exclusively using, at that time, the soon-to-be outdated arc lamps. The evolution towards using Tungsten lamps enabled the company to leave the film market to the major companies like Philips, and devote their work to theater (stage) and architectural lighting which was led by Strand Lighting.
It was soon to be the Disco era, psychedelic oil-based effects, an orgy of gobos and colors, the beginning of showbiz, and its dedicated and specialized lighting. Between these different uses of lamps, Jean-Charles quickly understands the importance of the new discharge lamp, the HMI by Osram and the MSR by Philips that were available in the late 1960s
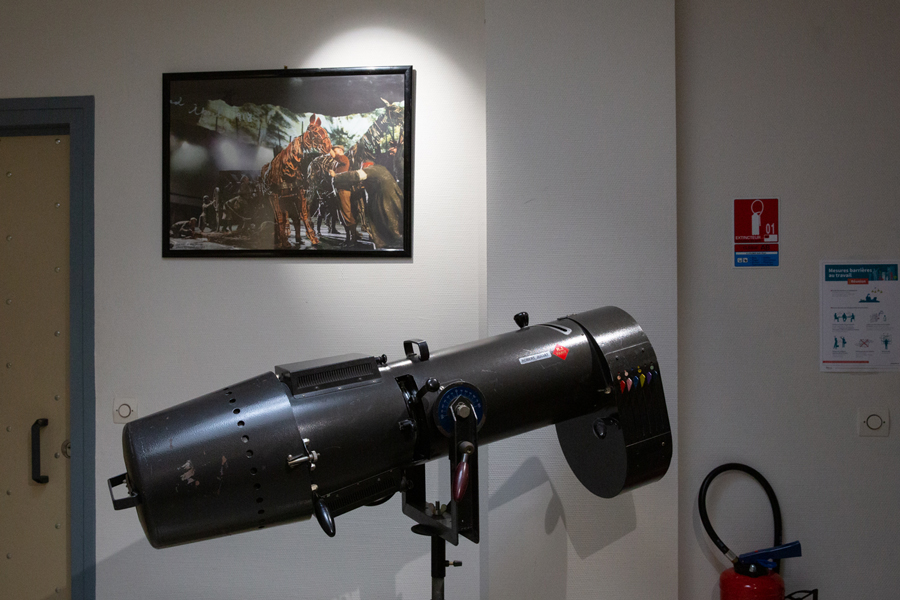
The first HMI followspot, Pixie, appeared in 1976 and put RJ in the Hall of Fame of entertainment companies. Little by little it replaced the steel beast carbon-arc Super Trouper, made famous by the song of the same name by the group ABBA in 1980.
It quickly became the companies’ trademark and evolved, with the progress in technology, with more punch and easier handling, along with the arrival of DMX protocol and the collaboration with AVAB.
This success paved the way for the constant growth of theaters and entertainment, encouraged by Jack Lang French Minister of Culture in the 1980s, and the development of Fresnel, Plano-Convex, and Profile luminaires. Long before Jean-Charles Juliat succeeded his father at the head of the company, Robert had already planned to leave Paris and move the company to a renovated post-war farmhouse in Champagne-sur-Oise.
This factory continued to grow with the help of distributors such as Collyns, however, they kept their offices in Paris, and later in Saint Denis (just outside of Paris) for their clientele. French stars such as Claude Francois, Bougliones, and Coluche continue to live in memory in the hallways of those offices.
As the company became bigger it moved to the small town of Fresnoy-en-Thelle, it could then include everything necessary for manufacture, inventory management, big machines, customer services, logistics, and a research center. The company with its 10000 square meters and 70 employees has become an economic hub for this area.
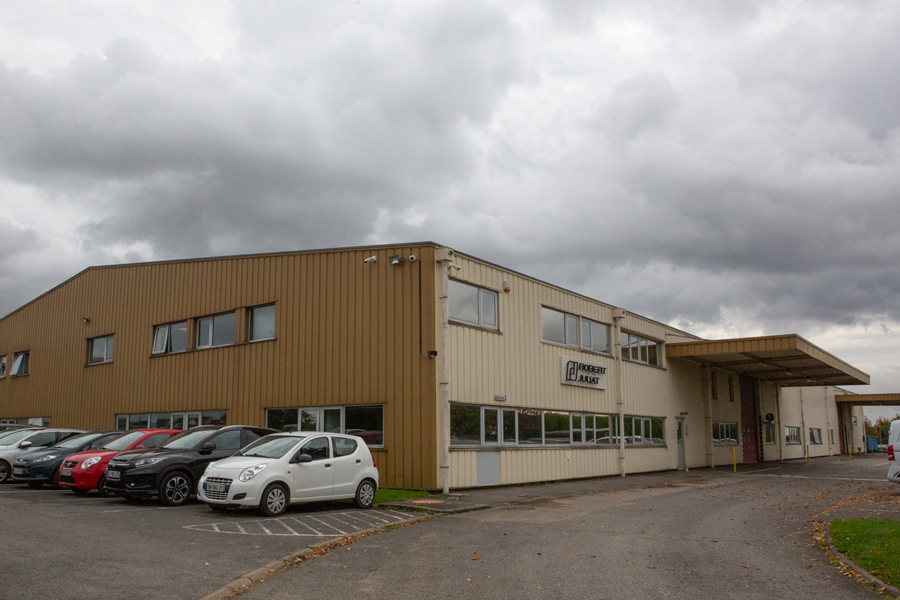
Followspots, the companies’ trademark, has opened the way for many other luminaires, such as the sacrosanct 614 and 714 profile fixtures, that have become the major reference of their type all over France. The expansion of theaters, encouraged by the Minister of Culture in the left-wing government, was going to fill up Robert Juliat’s order books like never before.
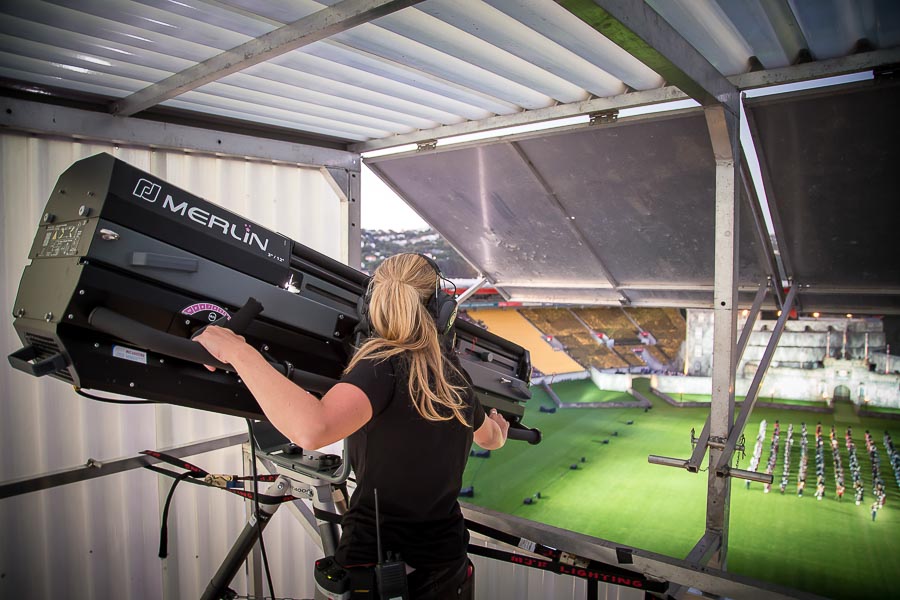
During the 1990s, business in France slows down, the company concentrates more on its exports. A distribution network per country is set up. For more convenience, in 1997, sales, communication, and administration are all done in-house at the headquarters in Fresnoy-en-Thelle.
The 2000s mark the beginning of global expansion. The “French Touch” is the reference in followspots, obtaining many awards in specialized Trade Shows. The Cyrano in 1999, Super Korrigan in 2006, and the Lancelot with its top-of-the-line effects comparable to the best moving lights in the industry used for the 2008 Olympics, the Merlin and now the Arthur, tested here in this magazine.
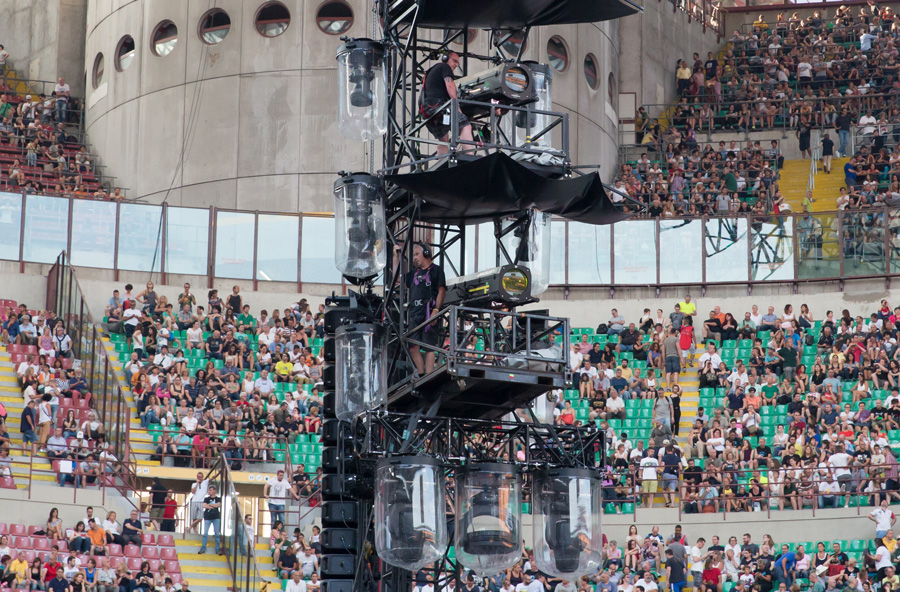
François, the American Son, joined his older brother Frédéric in the family business in 2003 and developed the American and Chinese markets. Although the followspots are their iconic luminaires, François with his vision of sales and Frédéric’s talent enables them to market more and more modern fixtures.
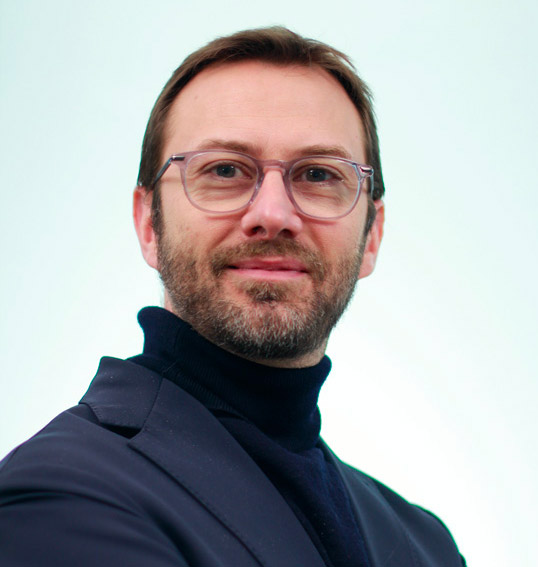
As of 2008, with François at the head of the company, they are on the brink of their third technological revolution. After the halogen and discharge lamps, electroluminescent diodes become the light source.
The Aledin profile, in 2010, was the result of a partnership and allowed the necessary amount of time for Robert Juliat to perfect the electronics and be self-sufficient. Two years later the Tibo and Zep were born, a giant technological leap forward for the homemade led light source.
In 2016, the Dalis bars, which are available in different models, encouraged the French company to collaborate with others who specialize in color sources. An engineering adventure that resulted in an innovative and exclusive luminaire, specially designed for live stage performances.
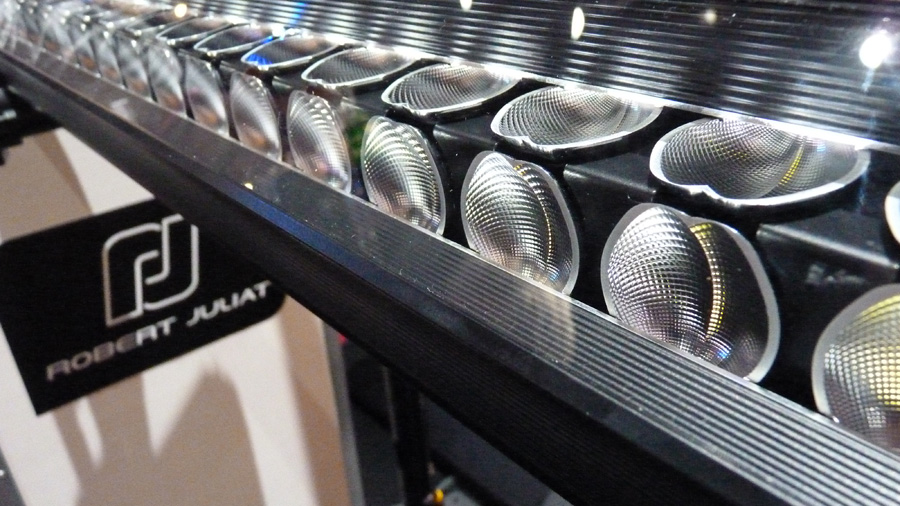
Along with the 150 units bought by the Bolchoï, and the awards obtained in 2015 and 2016, Robert Juliat has secured its position among the elite of high-tech companies in the entertainment industry.
After perfecting the use of the leds and mastering the slightest color, protocols (reseaux), and calculation algorithms, a whole new frontier opens up for Robert Juliat.
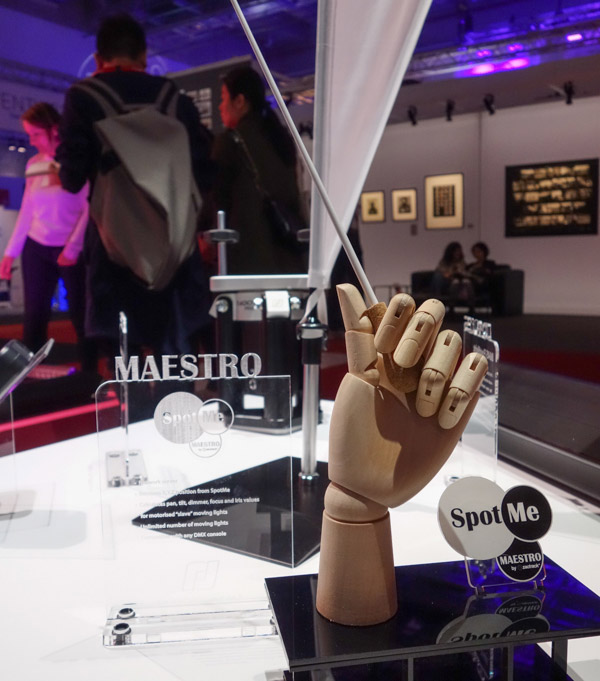
In 2019, with the collaboration of the Novum studio, the SpotMe system presented an “on-the-fly” tracking solution, innovative as ever. Today the research department is studying and dissecting the RDM and sACN protocols, to make the system more and more user-friendly.
Always looking for ways to improve and innovate Robert Juliat, the “grandfather” of lighting companies, is a maker of award-winning luminaires in France, and it’s what keeps them young, François, worthy successor of the family business, has kept the same excellence in craftsmanship as his forefathers and is amazed by the possible inventions of tomorrow.
General presentation of the company by François Juliat:
A quick history of the profile luminaire
After our visit to the past, Sévrine Zucchiatti, communication manager, and Ludwig Lepage, product manager, will walk us through the evolution of the Robert Juliat profile luminaire, and remind us of the very many innovations over the past decades.
This quite unique mix of traditional craftsmanship and state-of-the-art technology deserves our greatest respect for the innovations that have been made to the once “basic” lighting fixture used in theaters.
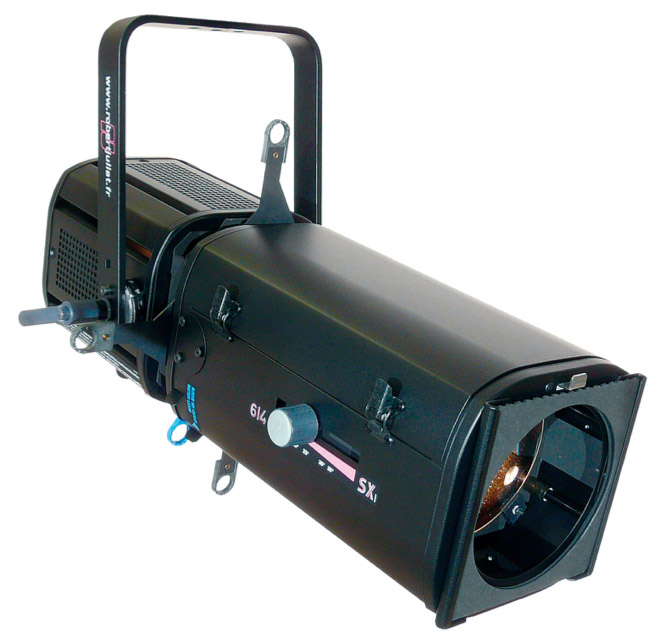
The 614SX is timeless, the quintessential 1000W halogen profile is over 30 years old. For generations technicians have memorized the positions and uses of the “knobs” for the lenses, clamping the shutter blades in their position, inserting gobos and color filters (gels).
Not forgetting the maybe lesser known handles to unblock the yoke, the iris/gobo double slot, 8 blade insert, internal gel holder, and the possible barrel rotation. Over the years, numerous little changes, almost going unseen, perfecting the optics, mechanical fine-tuning, and different materials used to enhance its performance.
Later followed other models with the same basic features: the 613SX with a 28 to 54° zoom, the 611SX zoom of 11 to 26°, thus adding to the 16 to 35° zoom of the 614SX.
Then came 714SX and SX2, “SX” standing for their double condensor optics, the “2” meaning it can house either a 2000W or 2500W lamp, and a 15 to 40° zoom. The 710, 711, and 713SX2 have zooms of 10 to 25°, 8 to 16°, and 29 to 50° respectively.
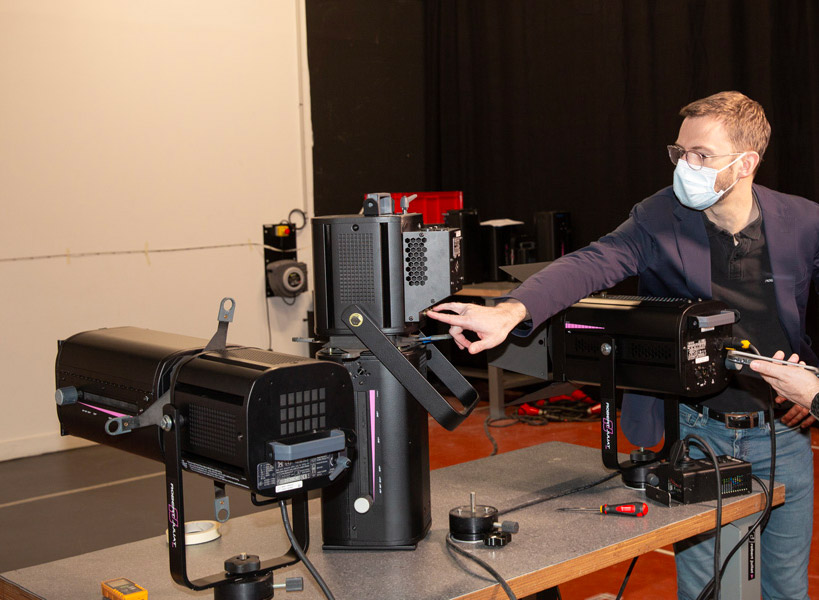
The Quincy, a lesser known model using an MSD 575W lamp, and the Artagnan 930,933 and 934NSX, using an MSD 2500W lamp, are an incursion into the use of discharge lamps, enabling the use of DMX to control the shutters and striking of the lamp. Widening the range available, always using the French know-how for generations.
With the advance in technology Robert Juliat had been looking into new led light sources, they were the first to use an 85W led block in 2010 with their Aledin. This type of led block could be used instead of, and in place of, the halogen lamps of the series 600SX turning the existing luminaires into more ecological ones.
The 3 models similar to the ones using tungsten lamps, 631,633 and 634SX had 40% less output, had room for improvement, and were quite a bit heavier, however, this new technology was ready for lift-off.
True to French engineering, Robert Juliat had always designed its own PCB*, including the control and ventilation modules, and Osram led modules. (*: Printed Circuit Board)
Aledin Video: This was the presentation of the totally new concept at the time, and is perfect to rediscover the 600SX profiles.
A few years later, in 2012, came the ZEP series, shown here, and/or the Tibo here in a new and improved model. The size and structure of the ZEP 641, 643, and 644SX2 were similar but with a bit bigger zoom barrel and the rear body of the 611, 613, and 614, using warm white or cool white 150W led module, complete with a menu and DMX connections or wireless option.
The result is very close to that of a 1000W halogen lamp and a color rendering of 70. The Tibo series, smaller in size are ideal for architectural lighting or sales conventions, they have slightly simplified optics and accessories, and an output of a 600W halogen lamp.
In 2018, the ZEP2 series was equipped with a new Osram led block, also 150W but with more output and a color rendering of 92. For the first time, the ZEP2 641,643 and 644SX2 had an output almost identical to the 600SX with tungsten lamps.
Using a 300W led block the ZEP 661,663 and 664SX2 were giving the traditional 2KW profiles a run for their money, the cool white version out-scores a 714SX2 with a CTB filter (gel).
Admittedly the ZEP series is longer and heavier than the tungsten ones, their led blocks are not adaptable in the standard profiles, however, the quality of the light output is such that they should be considered to replace an entire stock of profiles in a theater or on-hire.
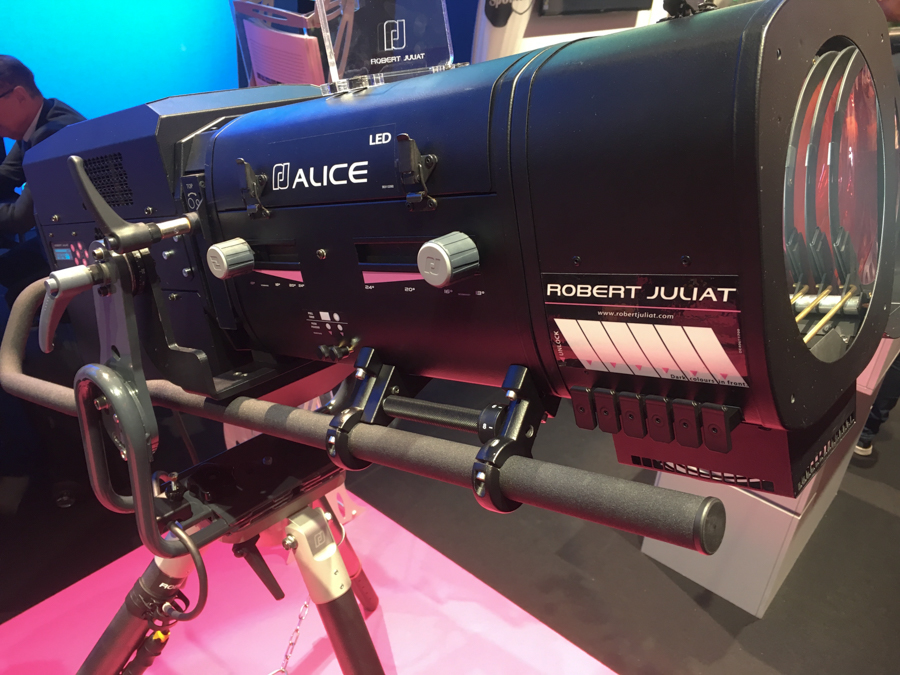
The Charles profiles, known as 961,963 and 964SX, are beginning to compete with the Artagnan which uses a 2500W HMI lamp.
These monsters, by their size and output, use a 600W 5600K led module, identical to the first led followspots, the Oz and Alice. Available since 2019, they haven’t had the exposure expected due to the Covid-19 lockdown, halting almost all shows and events.
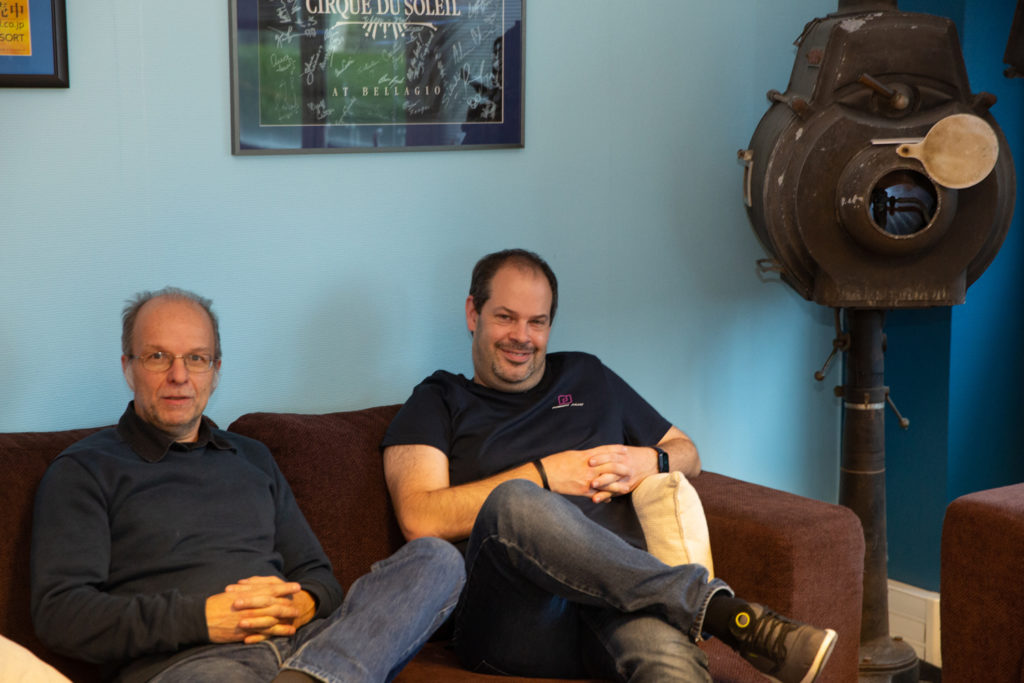
It takes more than a pandemic to discourage the French company. Their latest innovation is a led module interchangeable on the SX2 profiles, called Sully. Tested here.
It is overwhelming how the light output is far beyond that of the traditional profiles. Helping theaters to advance with this new technology, led sources, state-of-the-art networks, and an array of light sources, Robert Juliat continues to innovate with the Sully and Tibo HE series.
The factory strikes back
Even with the Covid-19 crisis, Robert Juliat, strong yet (modest?) humble, continues to carry the family colors. Robert Juliat, along with other French companies in the S1Bis sector, were helped by the UDFM association and the French government, they adapted their production line and were able to keep all their employees with partial unemployment.
Keeping their head above water wasn’t easy, comparable to the 2008 crisis or the post-war era. The 100-year-old company, with its diverse clientele onstage, shows, TV, theaters, and over 65% of exports was able to clear the rough waters.
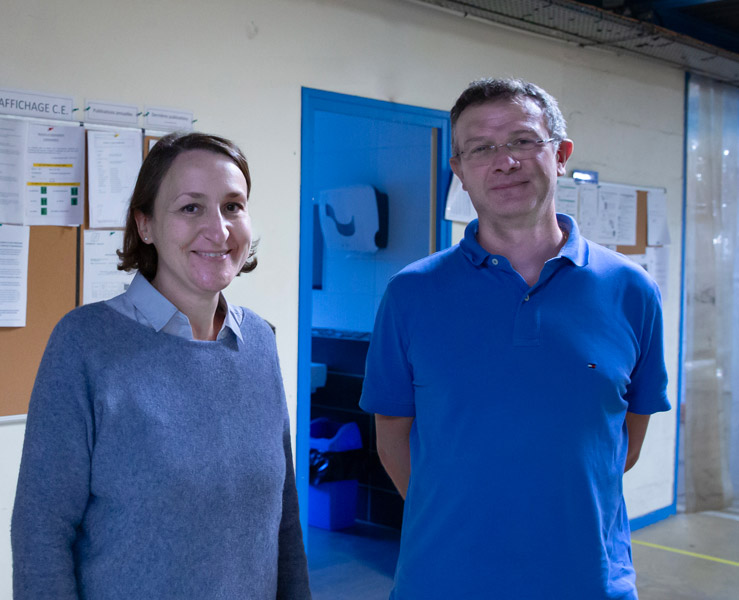
These difficult times have proven that the companies’ strategy is the correct one. It’s the mastering of many different technologies, reducing the number of outside suppliers, and a quick turn-around time that enables Robert Juliat to look calmly into the future.
Their work with led sources, the future of lighting, and the technological challenges to creating such products as SpotMe and the Sully 4C inspire lighting designers and technical directors
This DNA is obvious as we visit the maze of this factory. Séverine and Frédéric, our guides, have planned an in-depth tour, of the birth of a luminaire from a few grams of metal, a lens, some bits of plastic, and some electronics. Beforehand we must, as in a maternity ward, wear protective clothing as per the French regulations, including those very stylish shoe coverings.
The numerous and sometimes complex regulations are often questioned by many, however, they are the guarantee of quality and meet international standards. Robert Juliat has always been ahead of its time in terms of quality and standards, thus being able to easily export to North America or Asia.
The factory is buzzing with sixty or so employees, about 40 of them working on the assembly lines. The metalwork, with the automatic punching machine, is the heartbeat gobbling up pallet after pallet of sheet metal. The huge robotic arm switches between different tool bits. The sheet metal is bent and put into shape flawlessly nonstop with the grace of a dance routine, almost hypnotizing.
The old hand-driven machines on the side seem to be looking on as impressive cutouts are easily done, almost a relic from the past like all the bygone machine tools, they needed almost ninety people, to turn out a few hundred luminaires per day in the 1980s.
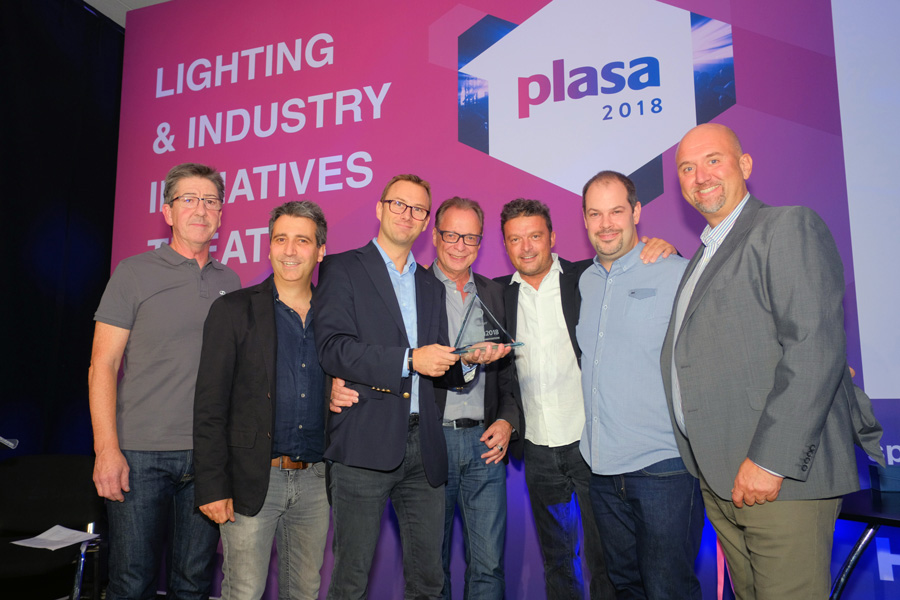
The company stands by its French craftsmanship, and know-how is what its demanding clientele is looking for. This also applies to being self-sufficient and using local suppliers, better turn-around times, and very rarely slowing production. Robert Juliat still has requests for the older versions of luminaires, even with the standardization in 2010. From the 1000W to the 5000W models (even though discharge lamps have practically become obsolete) over 3000 halogen luminaires were made in 2021.
There are no leftovers once the punching machine has finished its “meal”. It outputs the luminaires’ pattern complete with grids, and grooves, ready to be shaped. As soon as the series of luminaires, or types of luminaires with the same module, is decided upon the layout per sheet of metal is optimized to limit the amount of wasted or leftover metal.
All of the leftover metal, or scraps of metal, are recycled via their local suppliers, thus reducing their carbon footprint as much as possible.
The factory is like a mechanical wilderness, where the sounds of the punch press are similar to mating calls in the forest, and the folding of metal cut-out patterns are giving birth to luminaires. Metal bars, 6 meters in length, are cut and bent into the shape of the luminaires’ yoke, this is where metalwork meets show business. As different shapes are needed along the way, the machine operators change the different molds needed. Fresnel 310 sides, the back section of a Sully or the ZEP bases, these semi-automatic folding presses are outputting the parts that will become professional lighting fixtures.
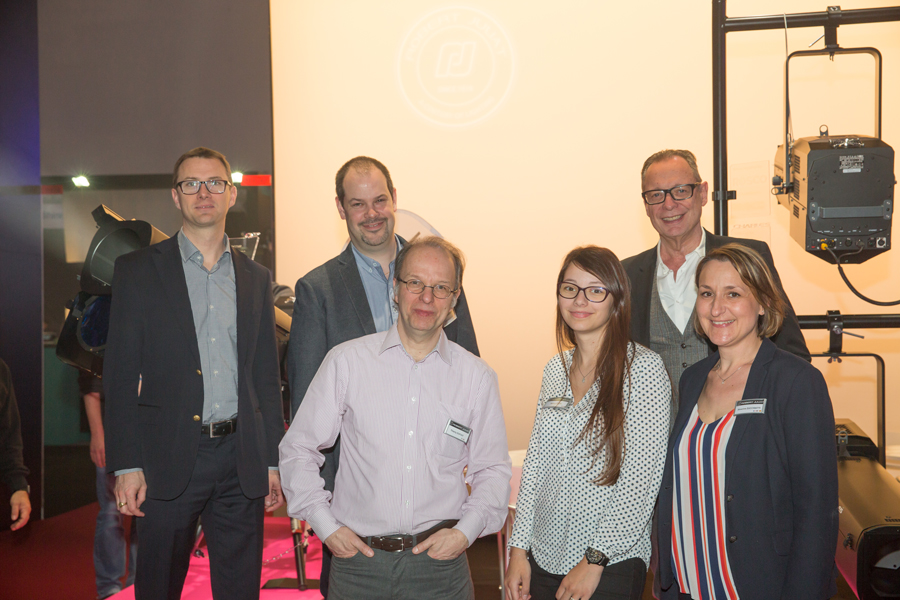
Adjacent to the machines, workers and specialized workers are riveting and welding in step. It is all about teamwork, co-workers depending on each other, and each generation passing down their knowledge and skills to the next. The PC (Plano Convex) Lutin, as per their historic conception are still handmade with care. The led luminaires, with their recognizable honeycomb grid, require other skills, the art of cabling and electronics. Repetitive tasks on the assembly line are waived by the engineering and the use of leds.
The Covid years had a major impact on the supply chain of raw materials. Wood, metal, textiles, and also paint, electronic components, and freight, in general, went askew. With the surge in investments for the upcoming summer events and last-minute orders due to the end of the fiscal year, our stocks were quickly dwindling. Luckily, the factory’s swift responsiveness, using identical parts for different models, along with local subcontractors, were able to meet the demands. All orders were delivered within 6 weeks, without employee overtime nor temporary labor being necessary.
It was barely visible that Covid had slowed production, except in the painting section where the luminaires were starting to pile up from the lack of paint. The de-greasing shop looked somewhat like a car shop, racks of luminaires were swallowed up into the chemical-free “vacuum” area to catch up with the backlog.
Painters apply solvents and powder in the extraction cabins, then like clothes pins on a washing line, the luminaire bodies go on a roller-coaster ride to the drying chambers in the basement then to the first-floor ovens. Once dry, the parts are separated by type and model ready to be assembled.
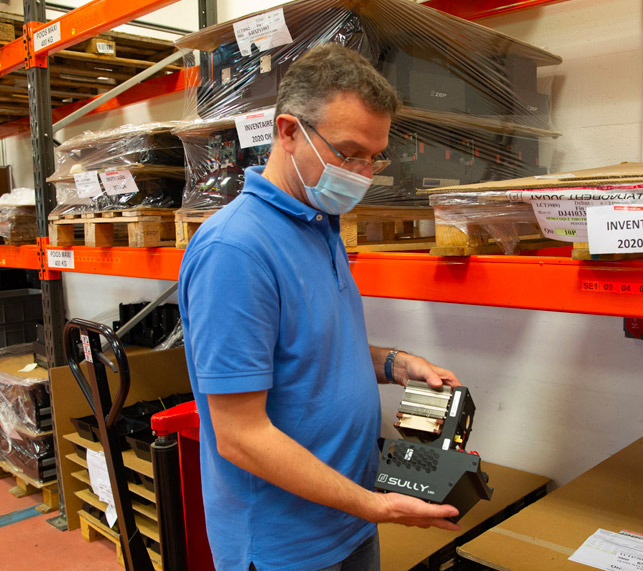
Up on the first floor, the mood is studious around the workbenches. Like an orchestra following music composed by the research department, electricians cable the power sources, opticians seal lenses in place, and electronics engineers couple components. The parts supplied by subcontractors are quality controlled and tested before their use. The light sources are ready and are just awaiting approval, before moving along on the escalators down to the ground floor for final assembly.
Although each step is highly specialized, they are all part of the overall picture. From creation to assembly, the production line is constantly adapting to change, something that s vital seeing that every three or four years a new technology emerges.
The engineers are raised on mechanical precision, thrive on industrial electrics, surf on electronic waves, and dream of new optics. They have the knowledge, the know-how, and put it all together with care to make a product that is efficient and timeless. This mastery of the components, and their track record, the luminaires are “followed” to ensure easy maintenance, repairs, and/or replacement of parts.
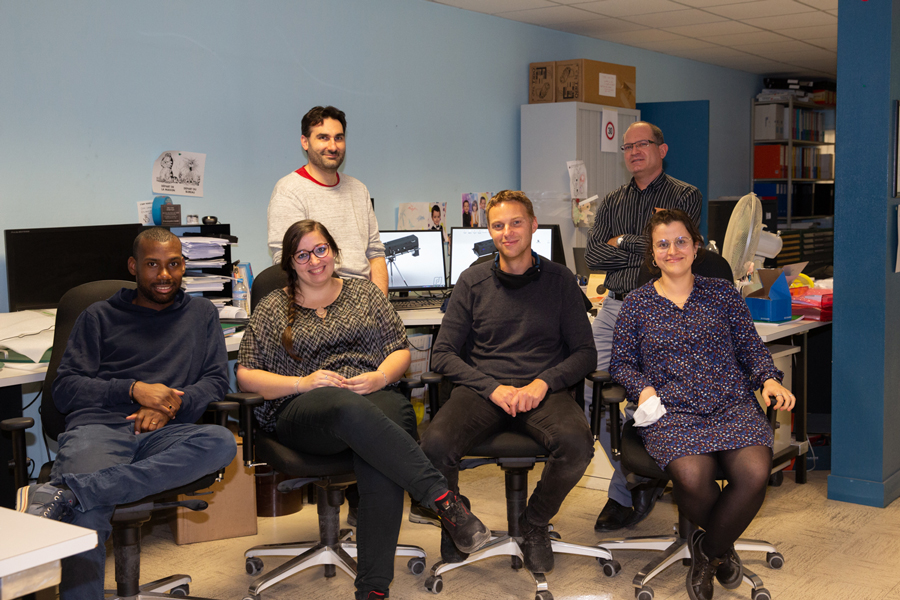
In a large room, using solar-energy lighting, a string of workspaces use pneumatic tools, and motorized hoists on beams to move the bigger heavier parts.
Depending on what has been ordered, from the light source to the accessories, all of the pieces gather to form either the small Lutin or the impressive Lancelot luminaire. Each one is checked one last time in the testing area, before being carefully packed into boxes, unless it is sent off in a flight-case made to measure by our nearby trusted partner, LikeCase.
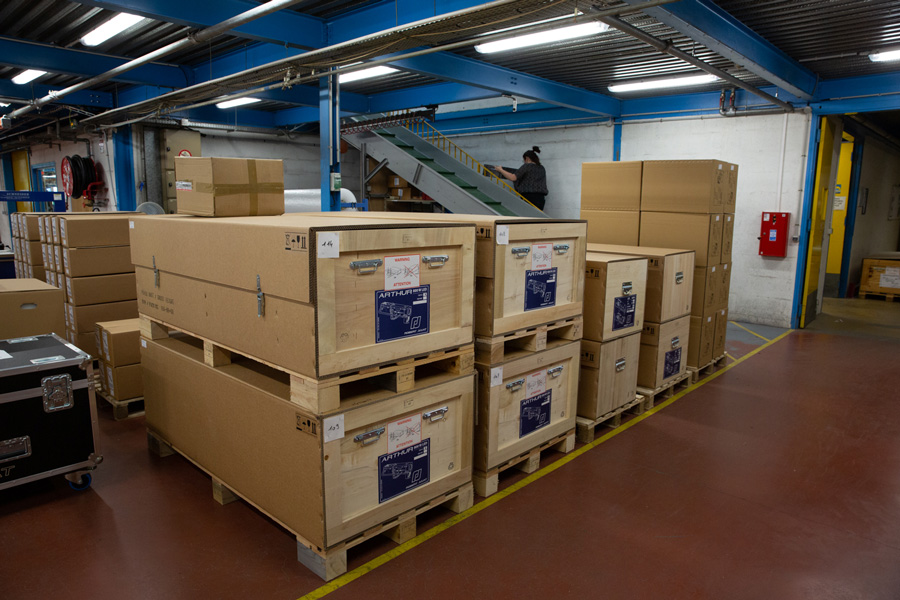
Our story has come to its end, a historic adventure, both human and industrial with one of the last great names in French lighting companies. The rest of the day was spent in the Research and Development offices, soaking in the research on PID RDM by Thierry Dupont, and the certification of the latest nodes to be embarked in the latest Sully.
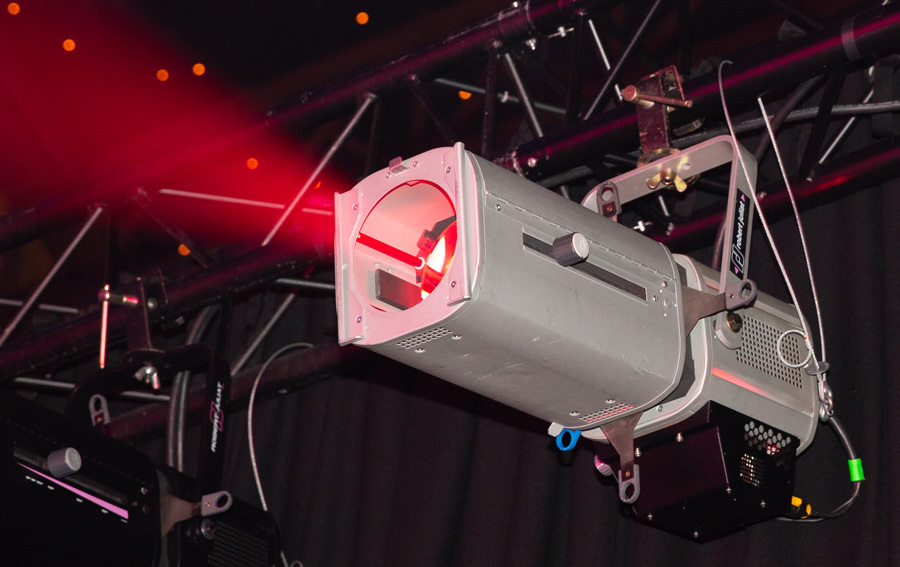
Seeing it from the users’ view is their strength, this is what has made the relationship between Robert Juliat and the client special for over a hundred years.
One hundred years of technical knowledge and research, not only makes great equipment, it makes Robert Juliat an ambassador of lighting.